Breakdown notes
Maintenance, production, safety, quality, inspection, audits and much more procedures can be digitised with the new Augmented & Connected Worker solution.
What is are Breakdown Notes?
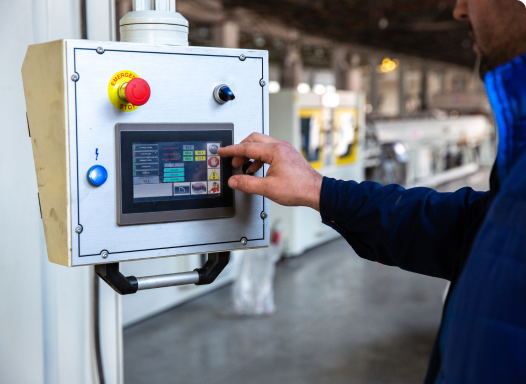
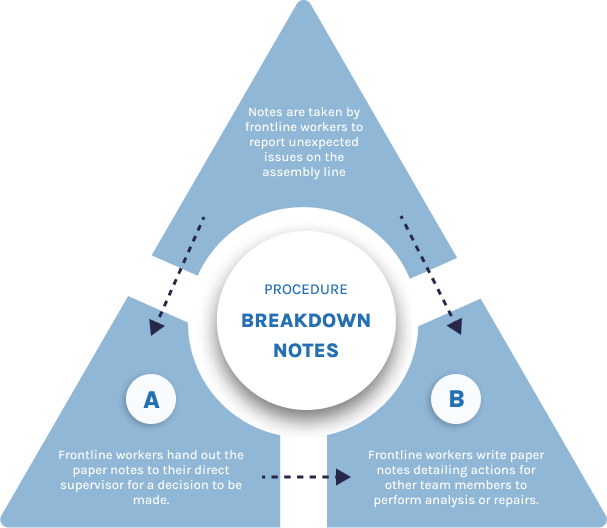
How are Breakdown notes implemented?
How the Connected Worker platform can improve the procedure?
Centralized Ticket System
Digital platforms allow for the integration of the ticket system that centralizes all processes’ information. Field workers can easily access their devices if they detect any strange behavior or failure that may turn into a breakdown. In addition, this will allow workers to share information in real-time and achieve a faster response.
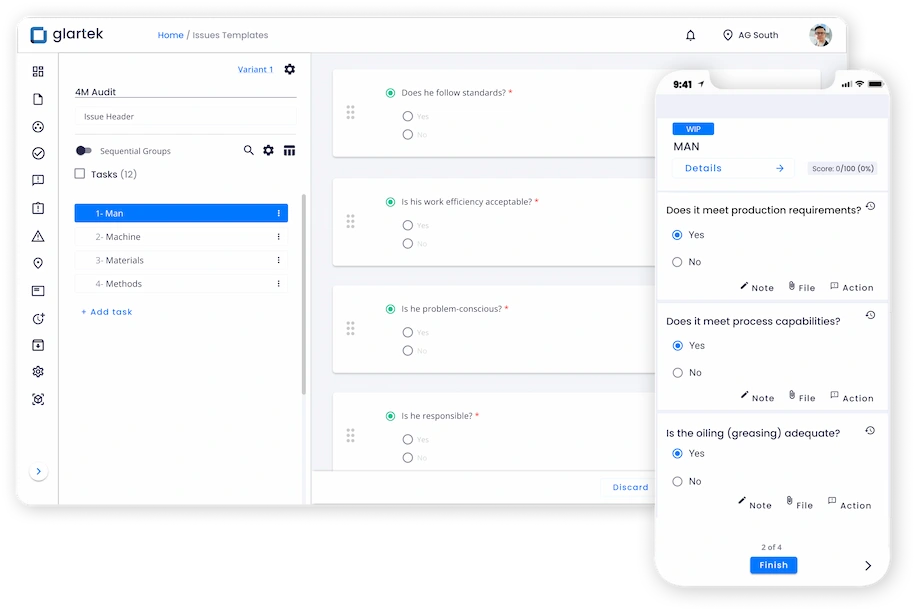
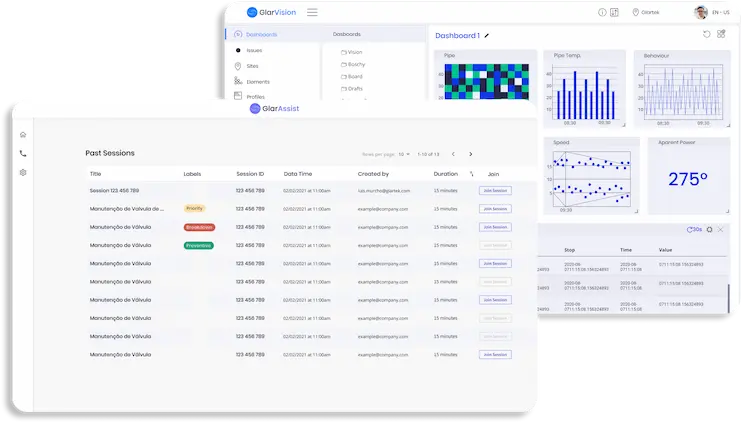
Visual Remote Assistance
When facing technical issues or breakdowns, workers do not always need to wait for experts. With remote assistance, specialists can immediately help operators resolve issues by making video calls, featuring a live chat and AR annotations.
Benefits
Of going from Paper to Digital Procedures
By accelerating and facilitating communication between field workers and specialists, there will be a faster resolution to breakdowns. As a result, this increases businesses’ overall productivity. In fact, by centralizing information and turning it into a digital format, it is possible to avoid breakdowns and reduce costs. Moreover, by adding a remote assistance tool, workers will be able to resolve problems in real-time and with the guidance of specialists, which will guarantee an increase in the first-time fix rate.
- COST REDUCTION
- FASTER RESPONSE TIME
- EFFICIENCY INCREASE
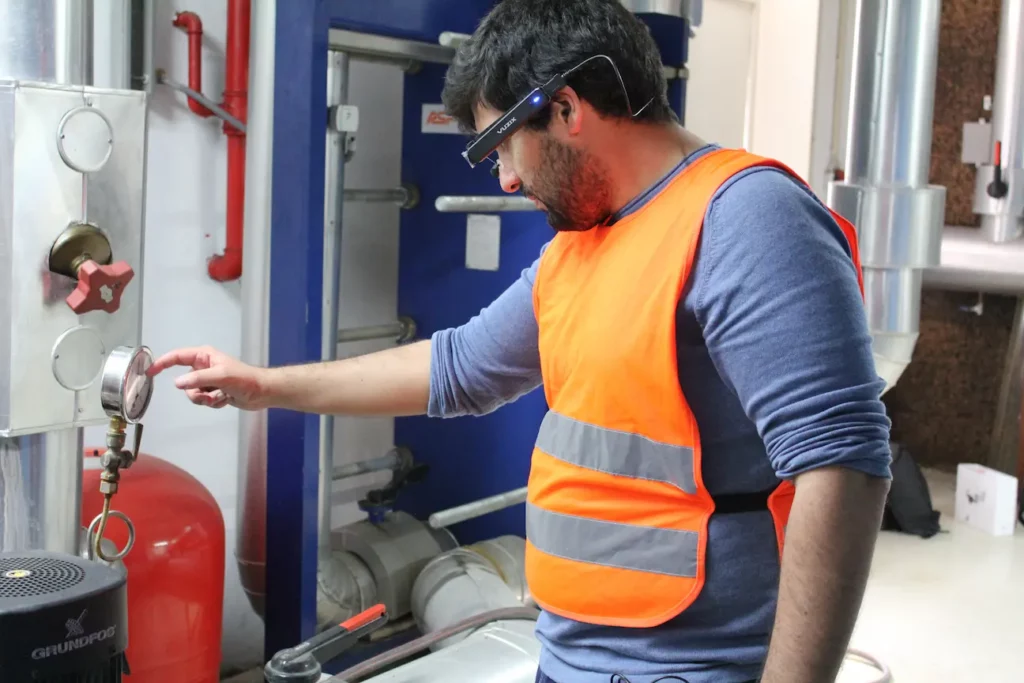