Meet the Waste Management Company
12+ years of experience
2 commercial plants in Spain
Over 200 professionals
The Challenge
The company’s reliance on paper-based routines and work instructions led to inefficient and lengthy training processes for new workers. This approach often resulted in incomplete skill acquisition, increasing the likelihood of operational errors and elevating safety risks, particularly among inexperienced employees.
Solution
The solution focused on three key points: digitizing procedures and work instructions, increasing guidance through augmented reality instructions, and providing skills management capabilities to managers.
Results
- 3x faster-training sessions
- 22% less training paperwork
- 0% frontline workers error rate
- 84% first time successful execution rate
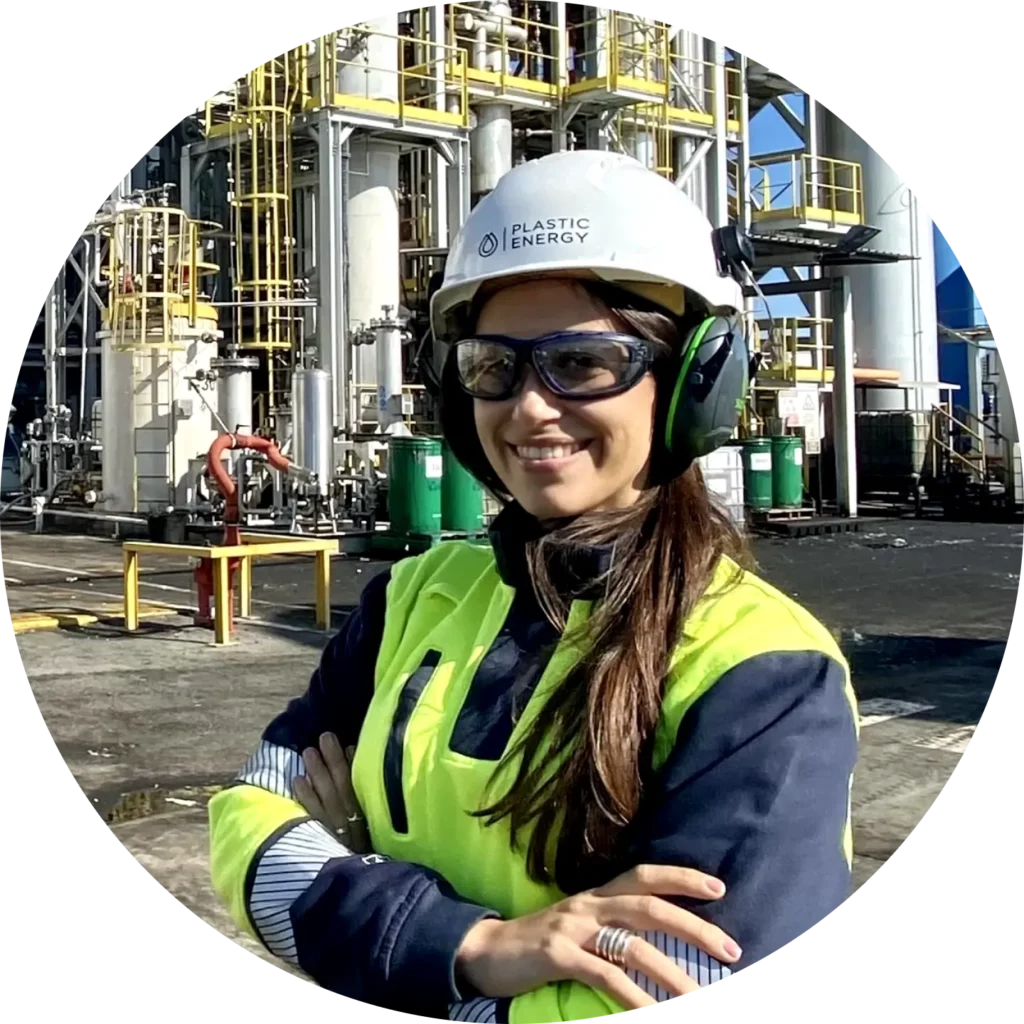
We’ve been able to decrease training times, requirements, and errors. Also, now we have real-time guidance supported by digital tools increasing workers’ autonomy leading to greater productivity and efficiency.”
María Sánchez, Process Engineering at Plastic Energy
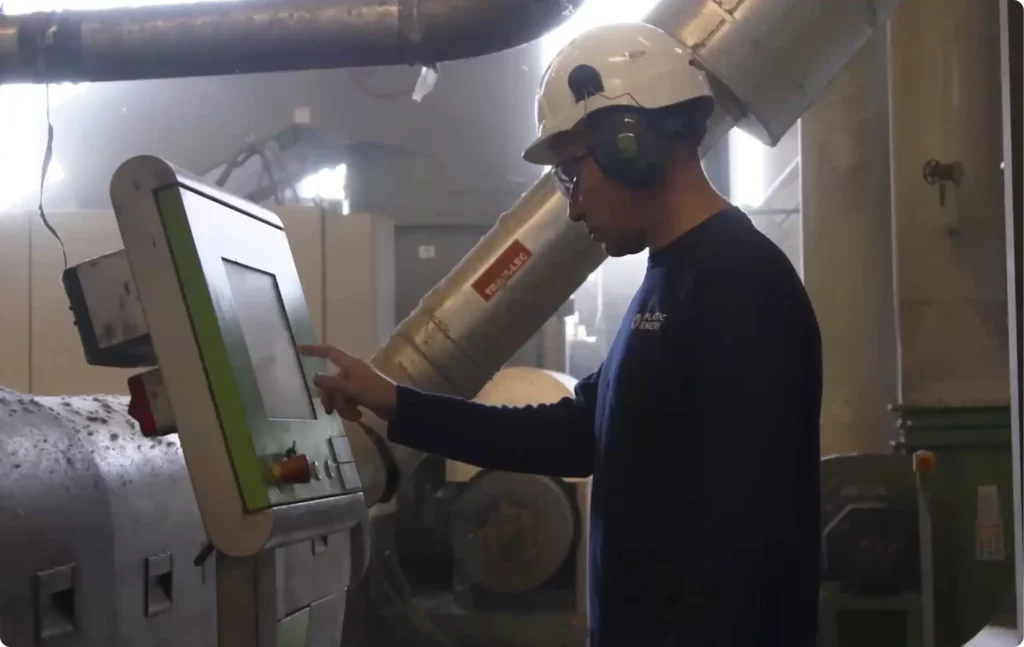
Lengthy, time-consuming, and non-contextualised training processes with lack of guidance
Before the implementation of Glartek’s solution, training procedures for new workers were carried out using paper-based documents, making them too complex and slow.
At the same time, the lack of clear and consistent guidance caused gaps in their skills development, inconsistent execution, and increased safety risks for new workers.
Improving training sessions efficiency while providing guidance for error-free executions.
Plastic Energy boosted training efficiency by digitising routines, resulting in 3x faster training sessions, a 22% reduction in training paperwork, and continuous skill development through effective skills management and tailored training programs.
Moreover, real-time, step-by-step AR instructions led to an 84% first-time successful execution rate for new operators. These improvements resulted in shorter training times, enhanced worker safety, and more reliable task execution.
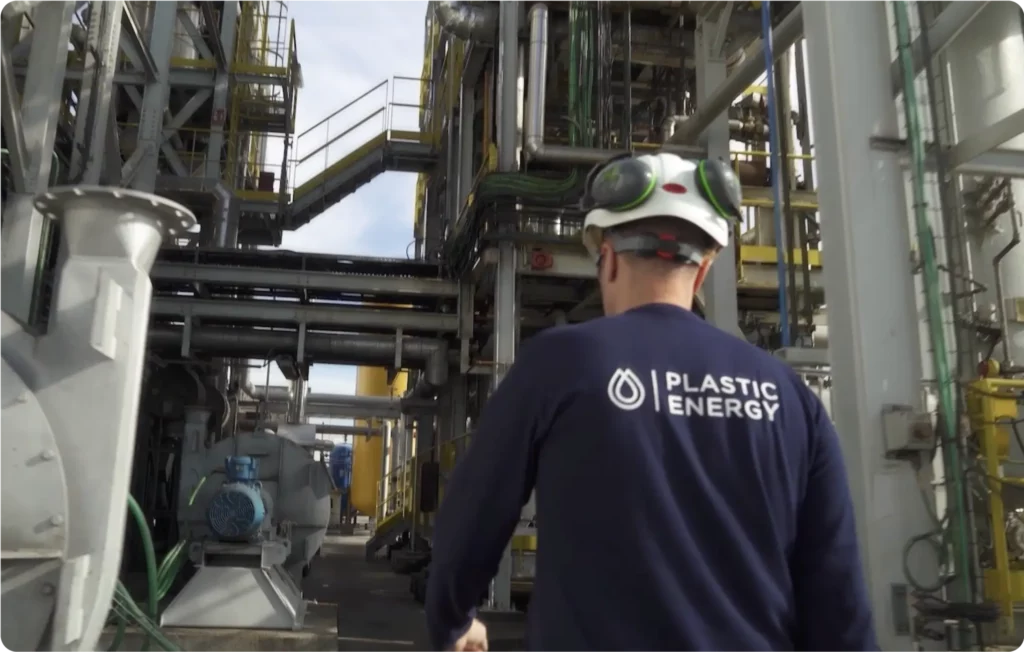
3x
Faster training sessions
22%
Less paperwork to prepare training
0%
Frontline workers error rate
Watch now
Watch full Plastic Energy testimonial video below and ear this Connected Worker success story from themselves!
Play Video
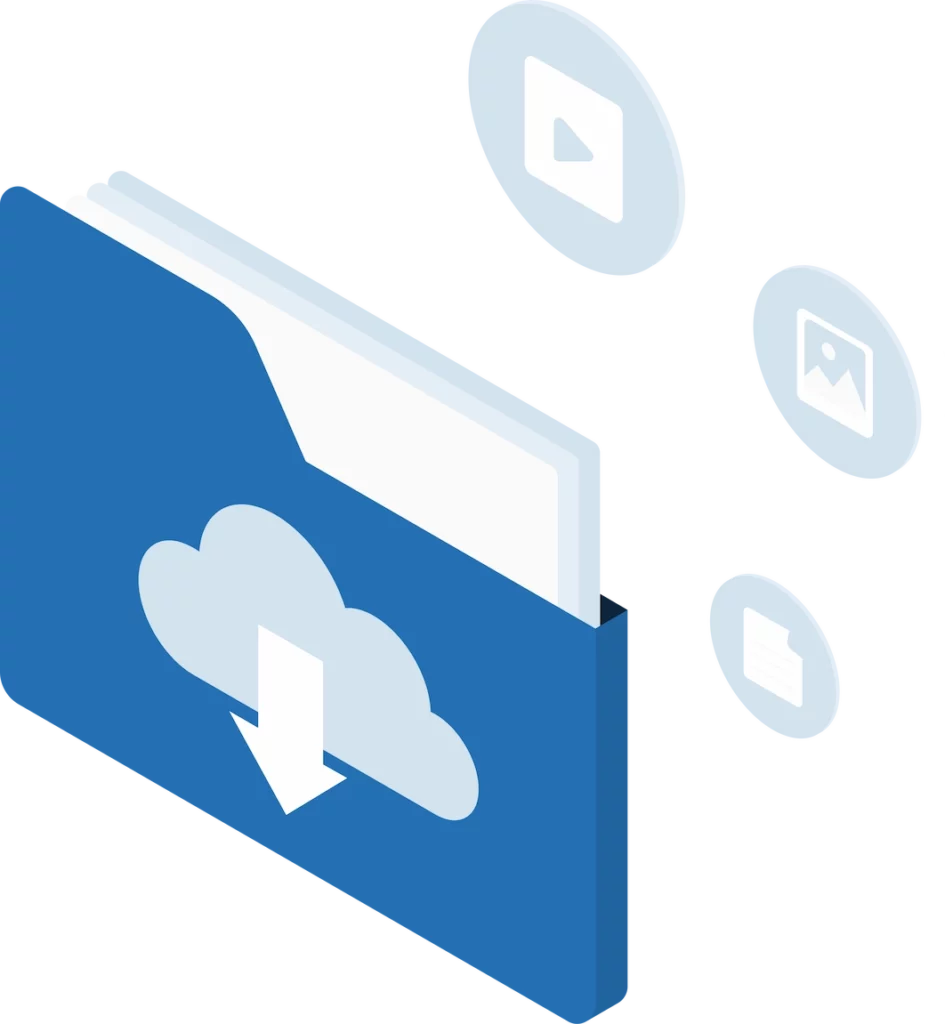