Meet one of the largest manufacturers of high-quality laminates.
Founded in 1959
+200M turnover
+100 employees
The Challenge
Sonae Indústria aimed to digitise its manufacturing processes to address a long-term challenge: managing a future plate 500km away, operated solely by frontline workers with no on-site management. To test Glartek’s platform capabilities, they implemented it in their current facilities, revealing key inefficiencies: outdated paper instructions, slow issue identification, risk of maintenance errors, and inefficient training and integration processes.
Solution
The solution focused on three key improvements: Centralising operations for real-time monitoring and management, digitalizing workflows to minimize errors, and implementing competency management for efficient training and onboarding. This approach empowered operators to work more autonomously and accurately, creating a more connected and productive operation.
Results
- 84% reduction in paper usage
- 42% faster issue resolution
- 25% reduction in downtime
- 3x faster onboarding of new workers
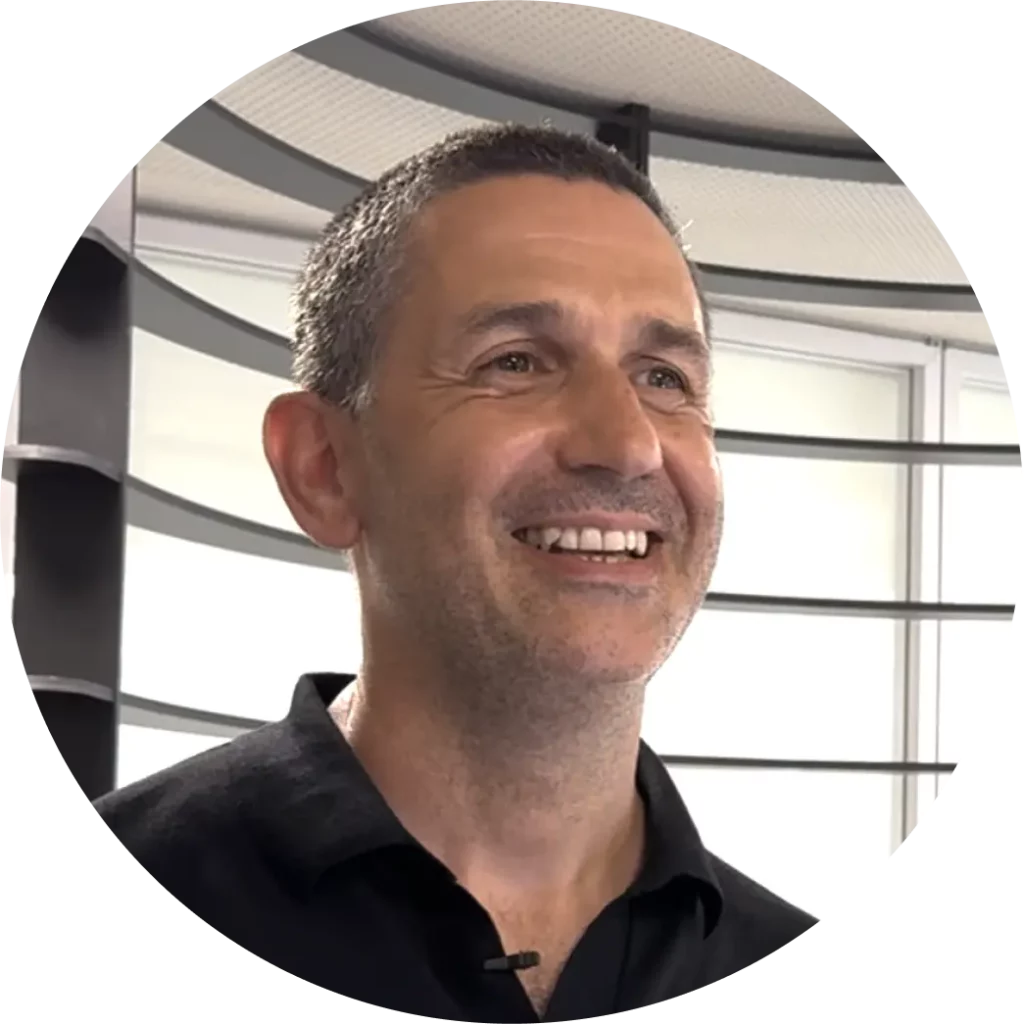
Glartek’s solution is more than just a support tool for maintenance or remote management. It is a comprehensive solution that enhances training, quality control, environmental control, safety, and the effective operation of our production lines.”
Miguel Nogueira, General Manager of Sonae Indústria
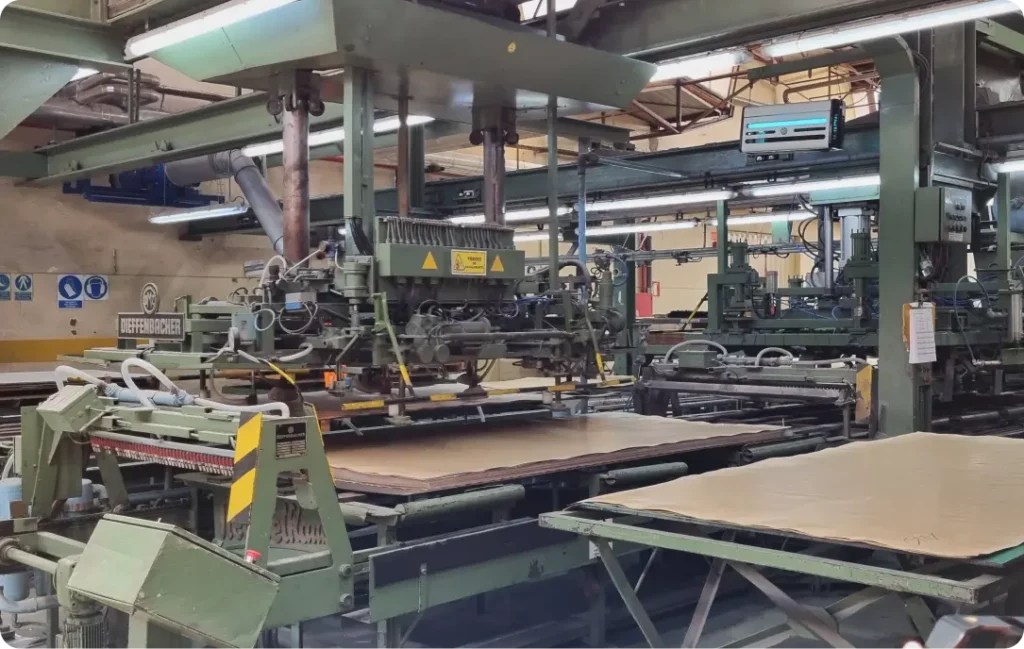
Outdated instructions, limited issue detection, and challenges in workforce training
Before implementing Glartek’s solution, Sonae Indústria faced several operational challenges. Their reliance on paper-based instructions caused inconsistencies and increased the risk of human error in critical procedures like preventive maintenance and LOTOS.
The absence of real-time monitoring delayed issue resolution and extended downtime. Additionally, training and onboarding processes were slow and inefficient, limiting worker integration, autonomy, and the capacity for on-the-job learning.
Digital work instructions, real-time monitoring and competency management
Glartek’s solution transformed Sonae Indústria’s operations by centralising all data and digitising workflows. Operators accessed step-by-step instructions for tasks like preventive maintenance, and LOTO on the production finishing line, reducing errors and boosting autonomy.
The platform also streamlined processes like safety checks, 5S audits, and PPE verifications, cutting paper use by 84%. With a skill Matrix and tailored training, onboarding was 3x faster, while real-time monitoring improved issue resolution by 42%, reducing downtime by 25%.
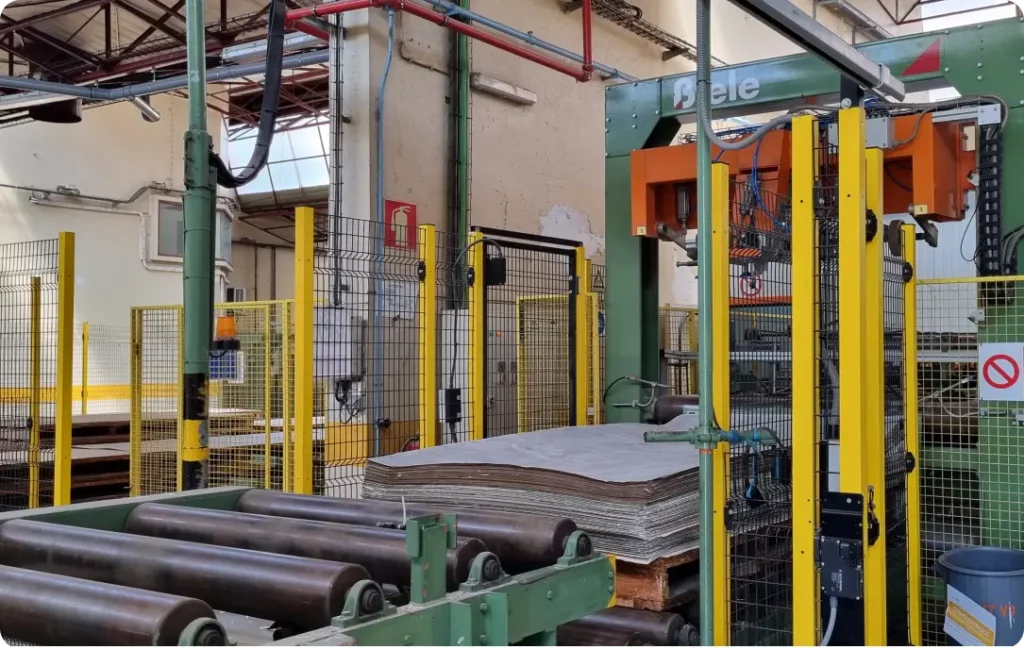
84%
Reduction in paper usage
3x
Faster onboarding of new workers
25%
Reduction in downtime
Watch now
Watch full Sonae Indústria testimonial video below and hear this Connected Worker success story from themselves!
Play Video about Sonae Industria video
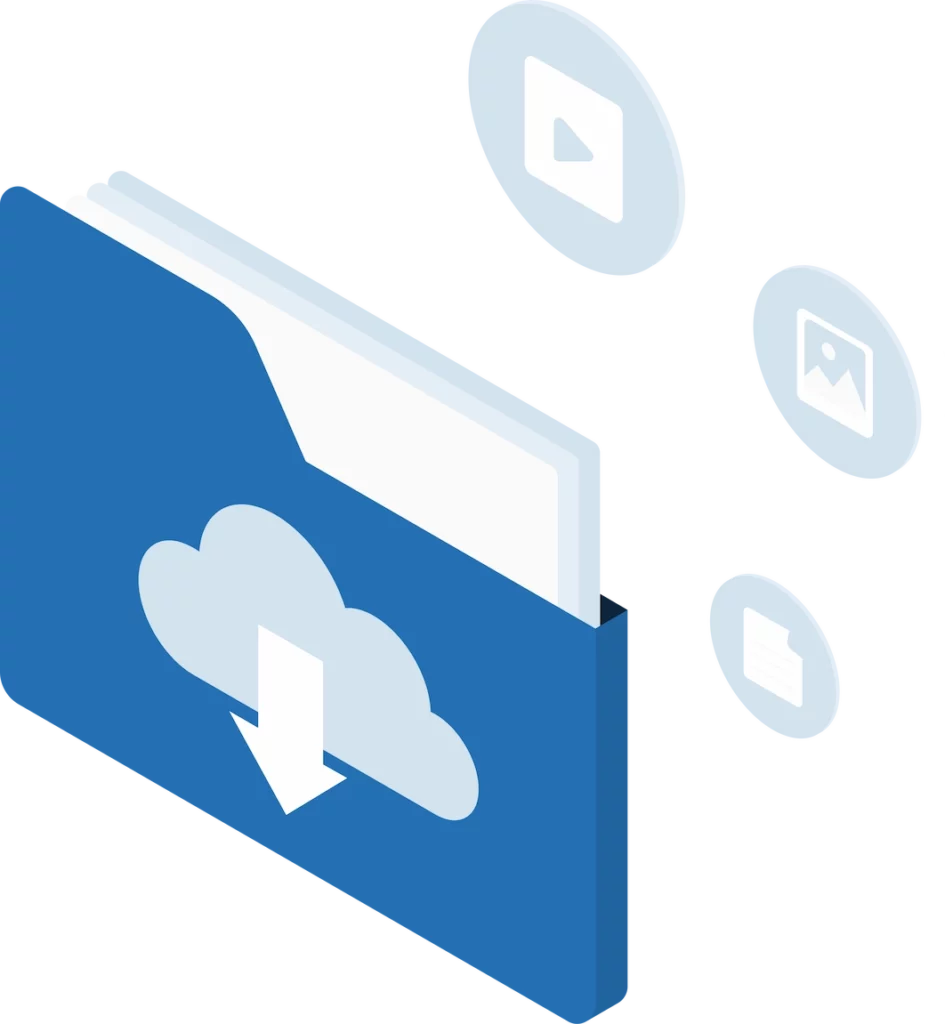