Meet the Waste Management Company
600 thousand tons of municipal waste
20% of all domestic waste
Over 25 years of experience
The Challenge
The company faced challenges with inefficient paper-based inspection, outdated documents, and limited access to critical information, leading to operational inefficiencies.
Solution
The solution focused on three key points: digitizing routines and work instructions, improving data recording and management, and centralizing all information.
Results
- 89% less time spent updating checklists
- 50% decrease in inspection execution time
- €246 710 total annual savings
- 93% less time to analyse inspections data
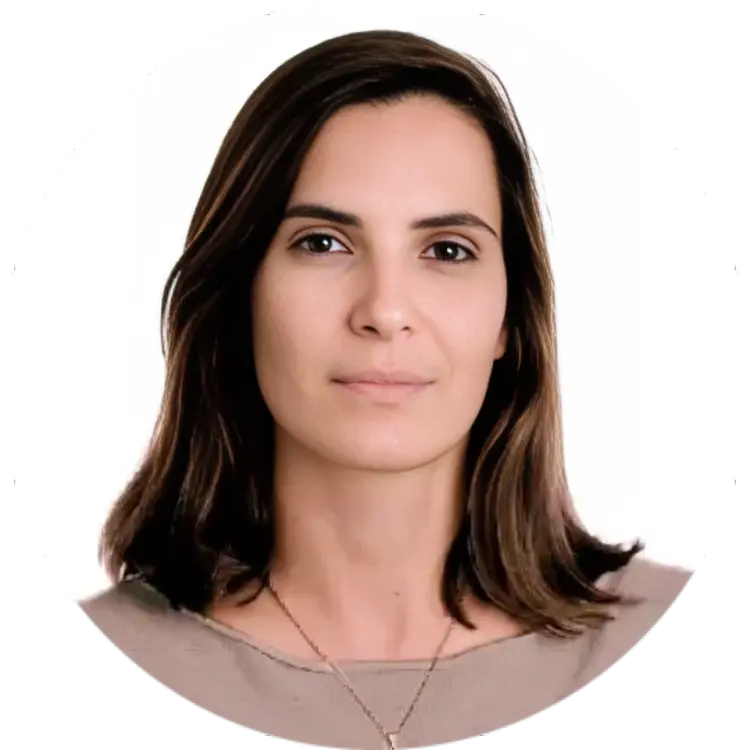
Glartek’s solution allows us to make an easier and faster diagnosis of the issues we have in our operations. The solution was very effective and met our expectations, so in the future our objective is to expand it to our different activities.”
Diana Tomázio, Innovation & Development Director at Valorsul
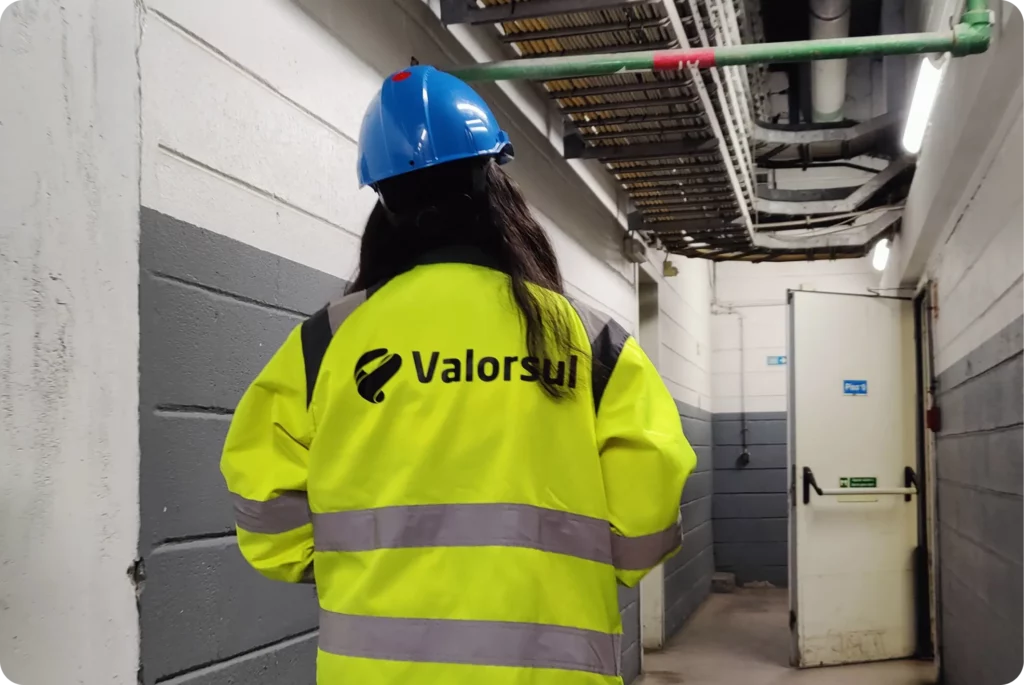
Outdated data, overlooked information, and limited access to critical equipment details
Before the implementation of Glartek’s solution, inspection rounds were conducted with paper-based documents that had to be filled out and handed in after the rounds.
Paper files, sometimes outdated, were not practical during inspections. Operators couldn’t access critical data, and collected data was not being used properly.
Streamling inspections, delivering substantial time and cost savings
Valorsul significantly improved efficiency by digitising its inspection processes, resulting in an 89% reduction in checklist update time, a 50% decrease in inspection execution time, and a 93% reduction in data analysis time.
These improvements resulted in annual savings of €246,710, reducing 2,335 labor hours and cutting labor and stoppages costs. Valorsul plans to extend this digital solution to other operations and additional facilities.
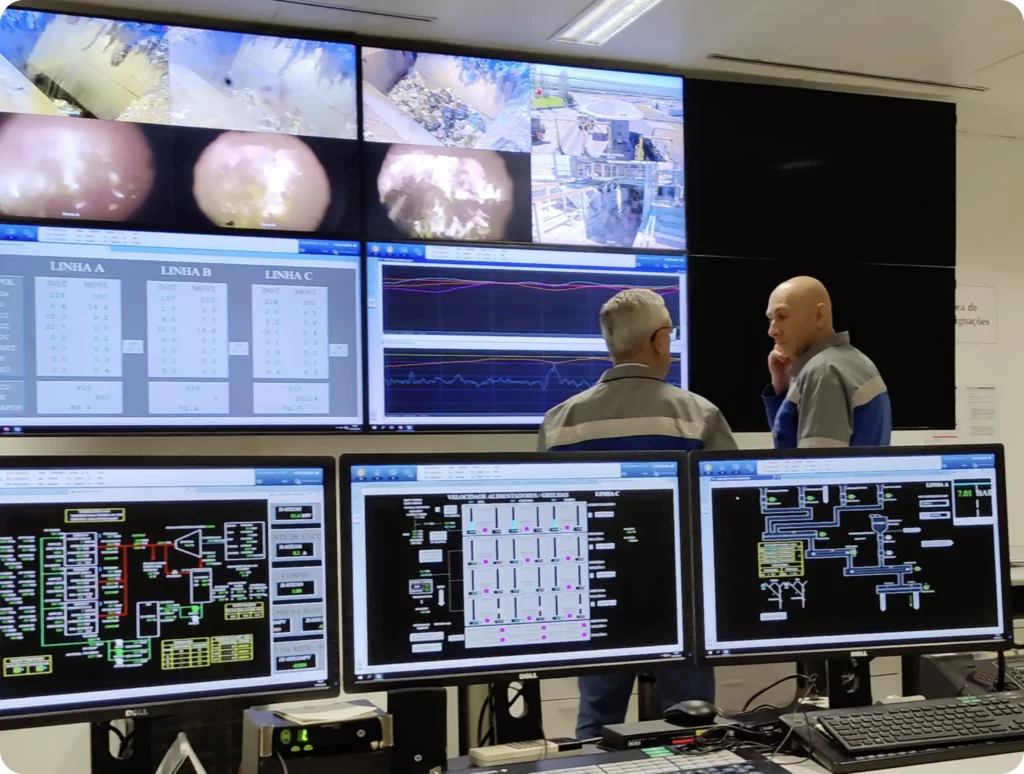
50%
Decrease in inspection
execution time
93%
Less time to analyse
inspections data
2x
Faster work progress
monitoring
Watch now
Watch full testimonial video below and ear this success story from themselves!
Play Video
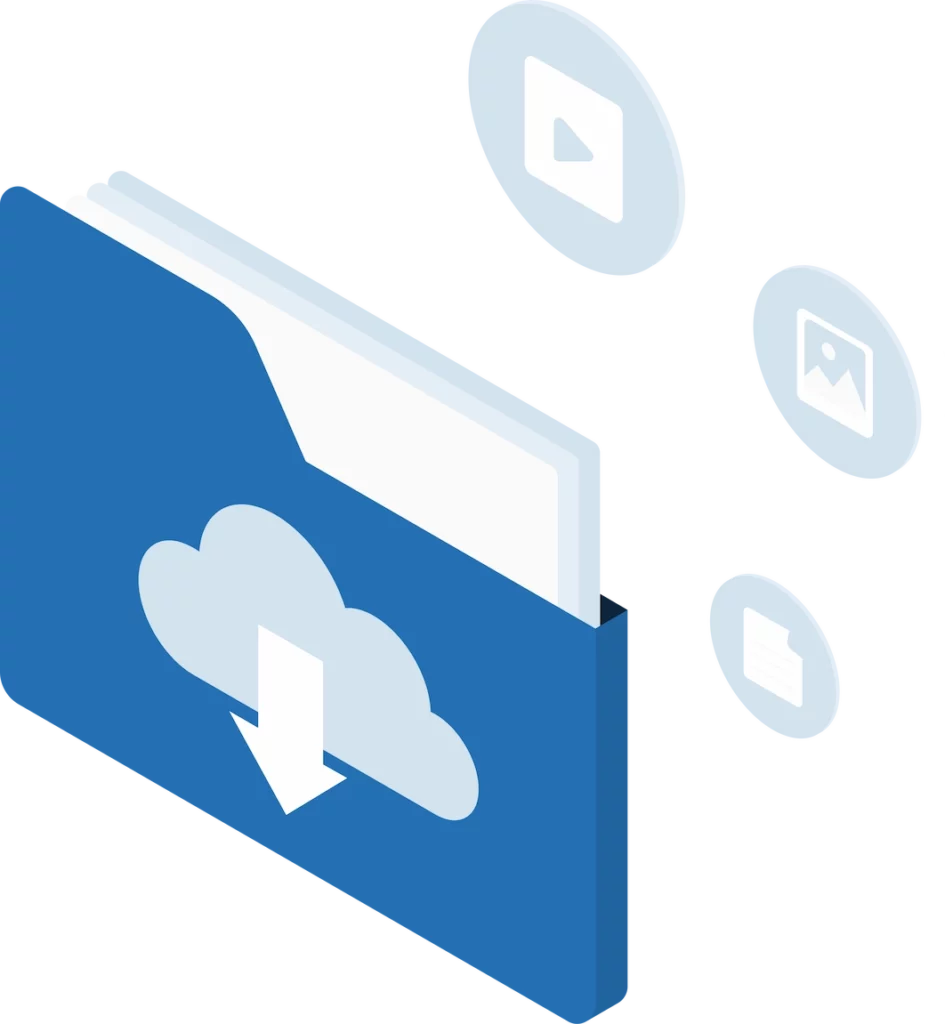