Poka-Yoke
Maintenance, production, safety, quality, inspection, audits and much more procedures can be digitised with the new Augmented & Connected Worker solution.
What is a Poka-Yoke procedure?
“Poka-Yoke”, which means “error prevention” in Japanese, is a process used to prevent and solve defects during production helping reduce the need for posterior quality inspections.
The process is relevant for any industry or situation in which error prevention is important. Some of the main errors targeted by this procedure include:
- Executional;
- Setup;
- Missing parts;
- Measurements.
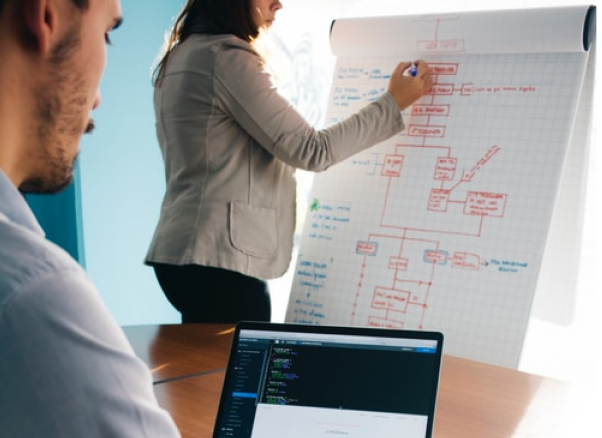
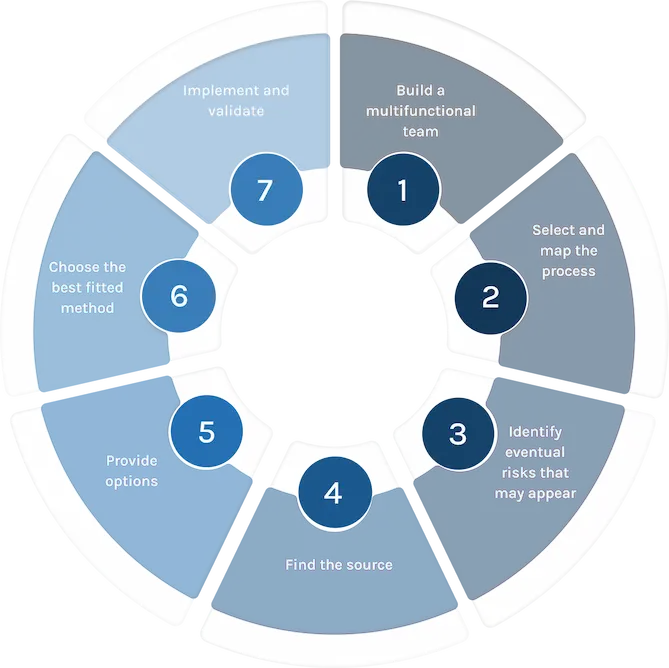
How is the Poka-Yoke procedure implemented?
One of the factors that sets the Poka-yoke procedure apart is that it makes the distinction between defects and mistakes. Where a defect is an error that is repeated and that may arrive to the customer, a mistake is an isolated error. Therefore, the process aims to reduce potential mistakes along the assembly chain, in order to reduce defects.
After the process is concluded, it is important to keep a continuous improvement mindset, in order to ensure that processes are frequently optimized and that results are achieved in the best way possible.
How the Connected Worker platform can improve the procedure?
Workflow Inputs
With Glartek’s technology, data is collected from each worker allocated to the process as well as times and steps are taken to execute it. The inputs include the conformity or non-conformity of the pieces. The information is furthermore summarised in a table for decision-making.
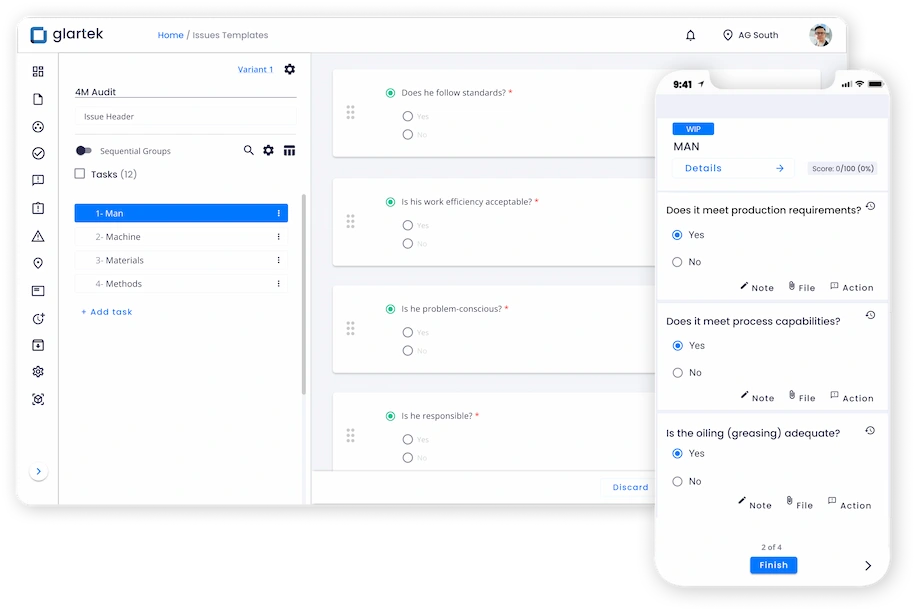
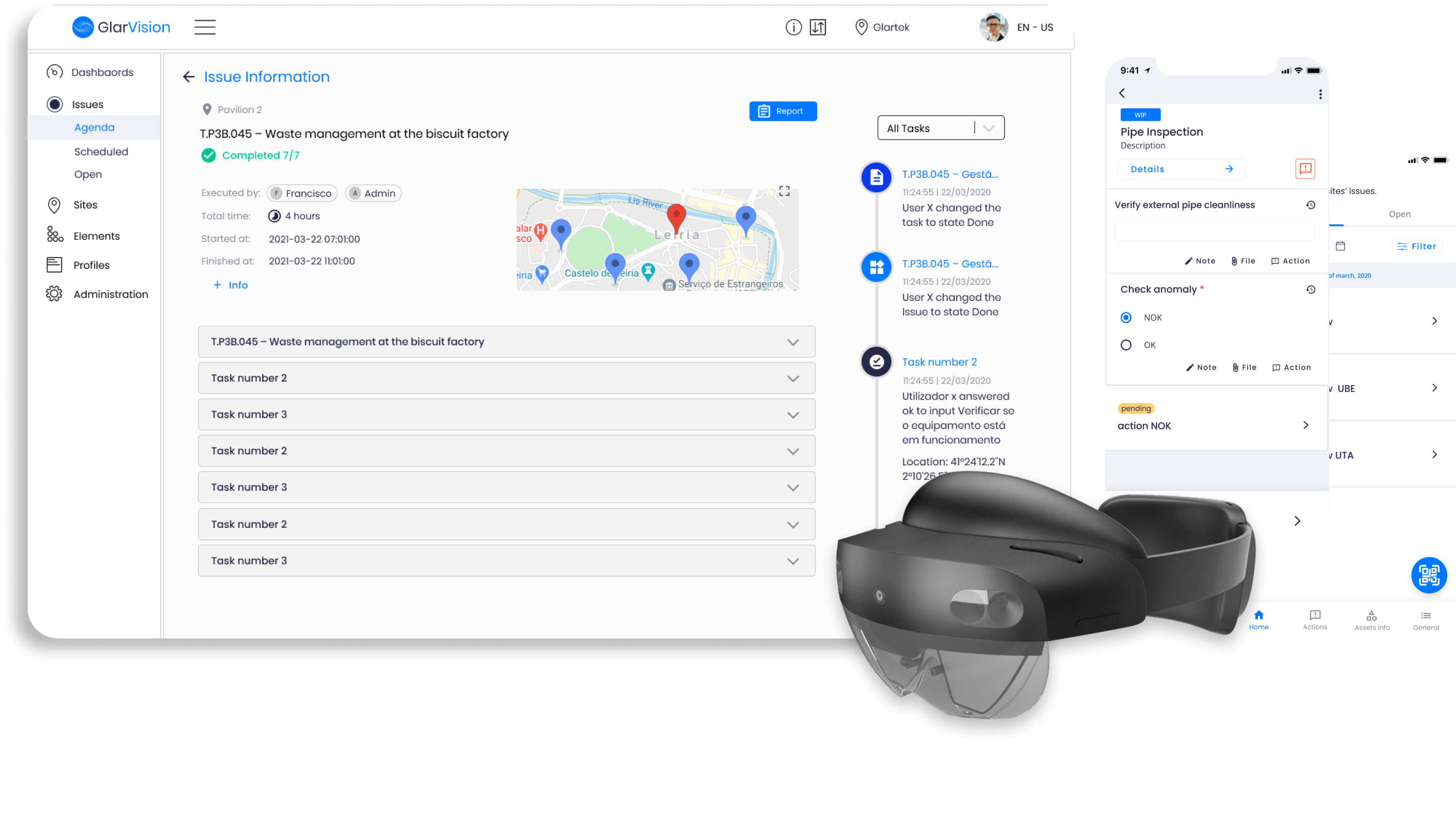
Visual Evidence
Our technology can provide execution visual support. An error is detected in a dynamic way, and workers are invited to validate if the product is OK or NOK. In addition, visual evidence such as short videos or photos can be submitted such as videos to guarantee execution.
Benefits
Of going from Paper to Digital Procedures
Digitized processes translate into a an improved mobility for workers that can now access more information about the execution of the process, in their workplace, increasing their know-how and productivity. The platform also translates into more information for managers, that is transformed into knowledge and becomes a huge support for decision-making.
- INCREASED CONTROL
- CONTINUOUS IMPROVEMENT
- REDUCED ERROR
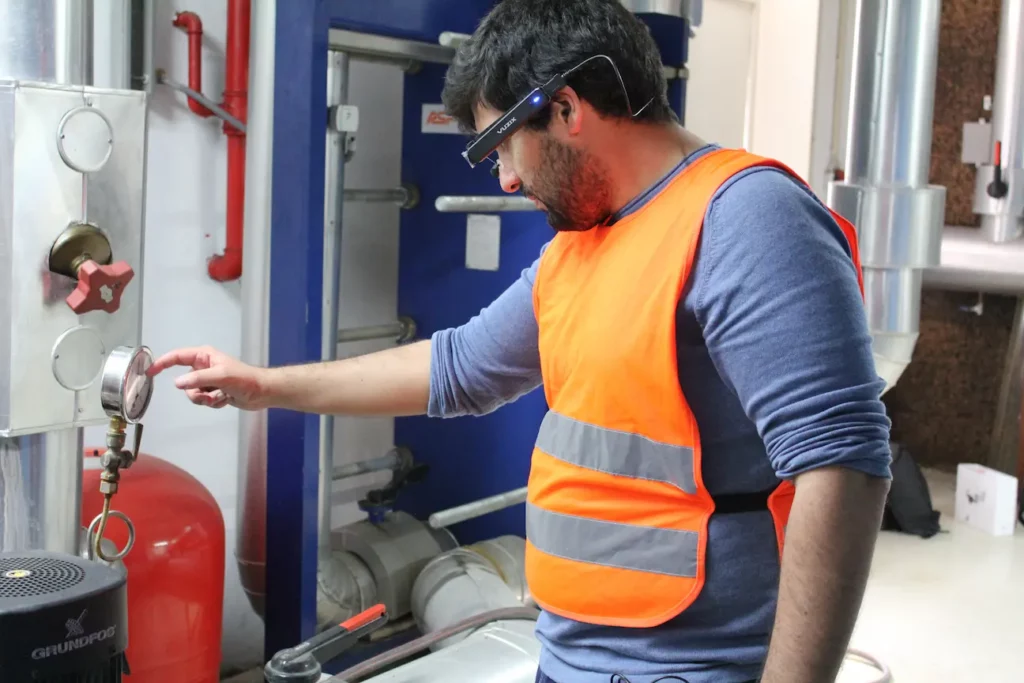