Plan-Do-Check-Act (PDCA)
Maintenance, production, safety, quality, inspection, audits and much more procedures can be digitised with the new Augmented & Connected Worker solution.
What is a PDCA procedure?
This process considers every problem as an opportunity for continuous improvement. It is a quality tool that aims to solve problems based on 4 different steps: plan, do, check, and act.
Plan-Do-Check-Act is a process that seeks to deliver change. The end goal focus on improving a project, a design, a process, or a specific action. In addition, it aims at implementing changes inside a company, gathering information to evaluate the change put in practice, and working towards continuous improvement.
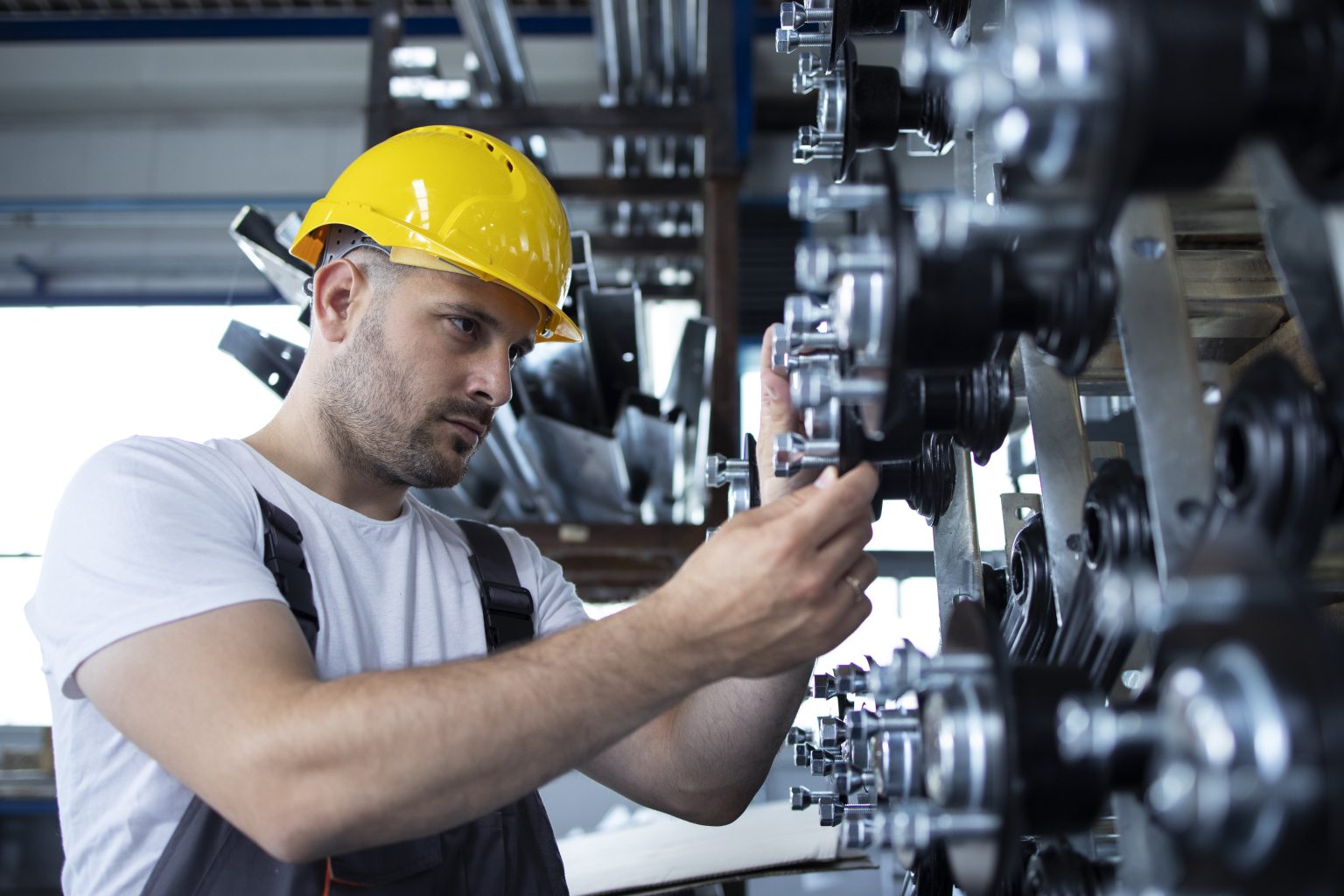
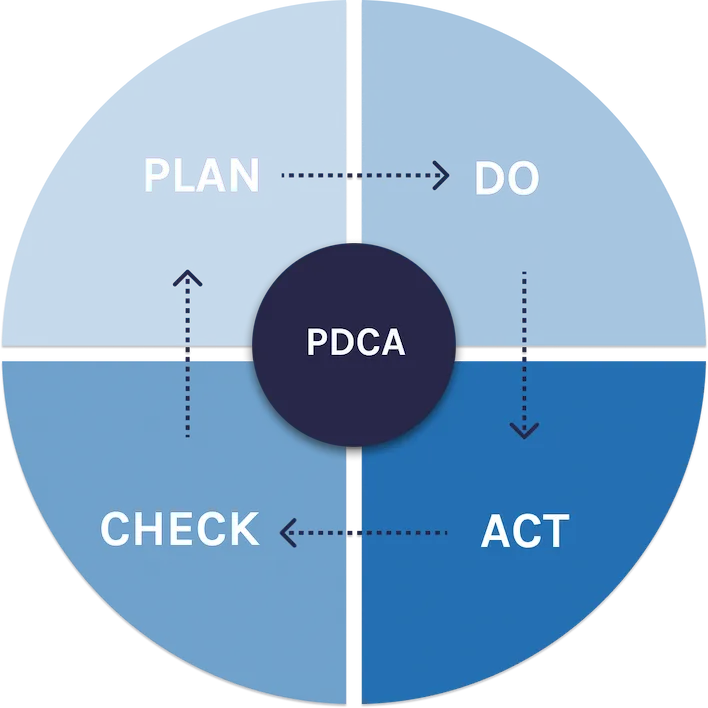
How is the PDCA implemented?
PDCA (Plan-do-check-act) is a four-step process to help review changes within a company.
Plan (Or “Analyze”): An analysis of the data seeks to identify an opportunity to improve a specific operation.
Do (Or “Perform”): goals must be defined to ensure there is an actual output that will be extracted from the PDCA process. Then, the organization decides on actions to achieve that same goal.
Check (Or “Monitor”): Monitor and evaluate results. The data assessment serves as the input for the next step in the cycle.
Act (Or “Improve”): Usually, this step is specific to each process or operation. However, most times it can result in the standardization of regular PDCA processes, in order to improve operations continuously.
How the Connected Worker platform can improve the procedure?
Centralized inputs
Businesses will have more visibility over processes, execution, and workers’ feedback by introducing a platform that centralizes information. As a result, this information works as analytical data to facilitate analysis.
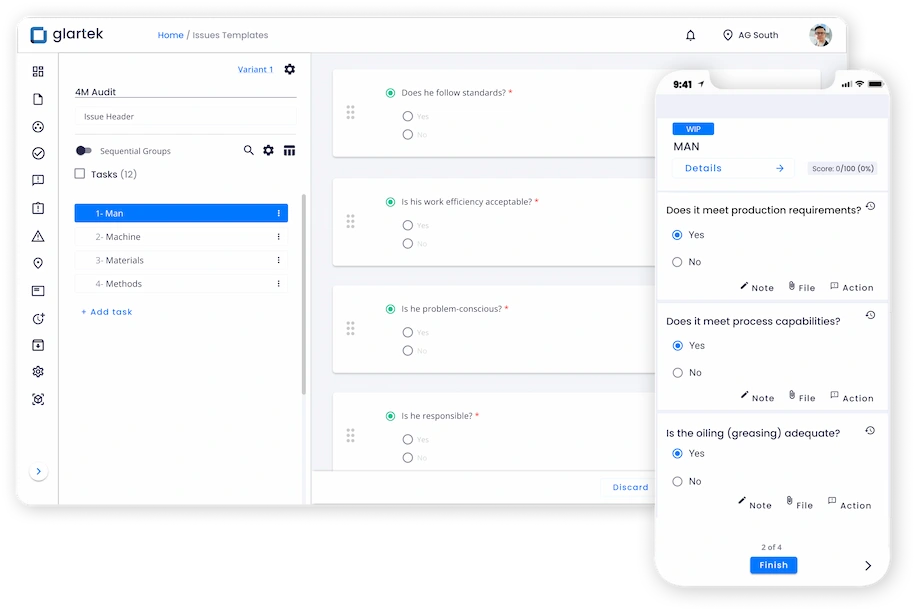
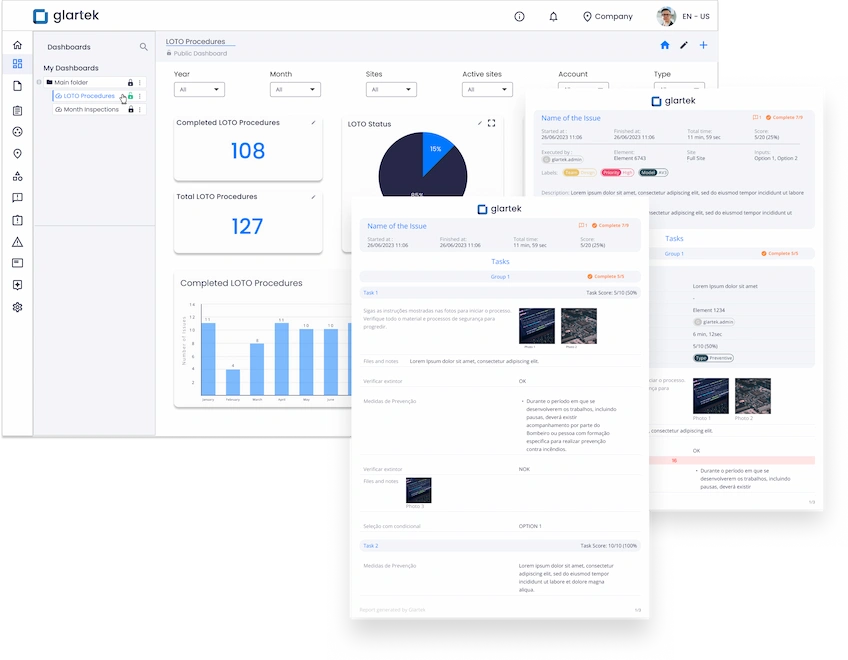
Automated reports
Glartek’s platform digitizes processes and organizes them according to different variables. Workers are provided with workflows to help them during the execution process. Finally, reports are generated with the different inputs extracted from the execution of the procedure described above.
Benefits
Of going from Paper to Digital Procedures
Thanks to this technology, processes are more efficient, helping reduce the company’s overall costs. As a result of workers being empowered, it is possible to have smaller teams and decrease the need for specialization. Finally, continuous improvement becomes key and the new focus.
- CLEAR INFORMATION
- REDUCED COSTS
- EFFICIENCY INCREASE
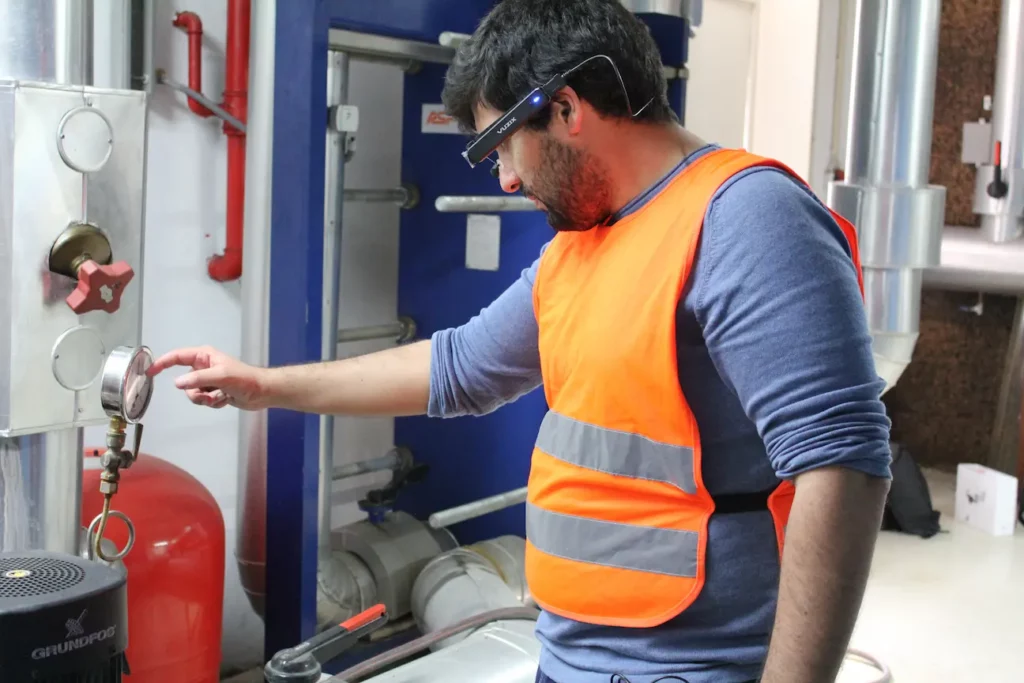
How can Glartek help?
Request your DEMO
It's time for you to join this New Reality
Start your Augmented & Connected Worker journey with us and become the leader of your industry.
