Training in the Industry 4.0
Amidst global competition and an aging workforce, manufacturers grapple with the urgent need for skilled replacements. To overcome the decades-long training cycle, they must adopt researched industrial design methods for faster, more effective training solutions.
A New Reality impacting training efficiency and reutrn on investment
These days, manufacturers face a series of mounting challenges. On the one hand, they must compete with overseas producers who manufacture at lower costs. However, at the same time, the aging workforce requires that young, bright but inexperienced replacements are quickly “trained up”. But this is where companies find the real obstacle: historically it has typically taken 20-30 years to train a new hire to fill high-level manufacturing jobs.
Faced with the challenges mentioned above, manufacturers need to provide more effective training to reduce this training cycle. That’s why it’s increasingly important to turn to the proven, researched, and scientifically valid techniques of industrial industry and instructional design when creating training materials.
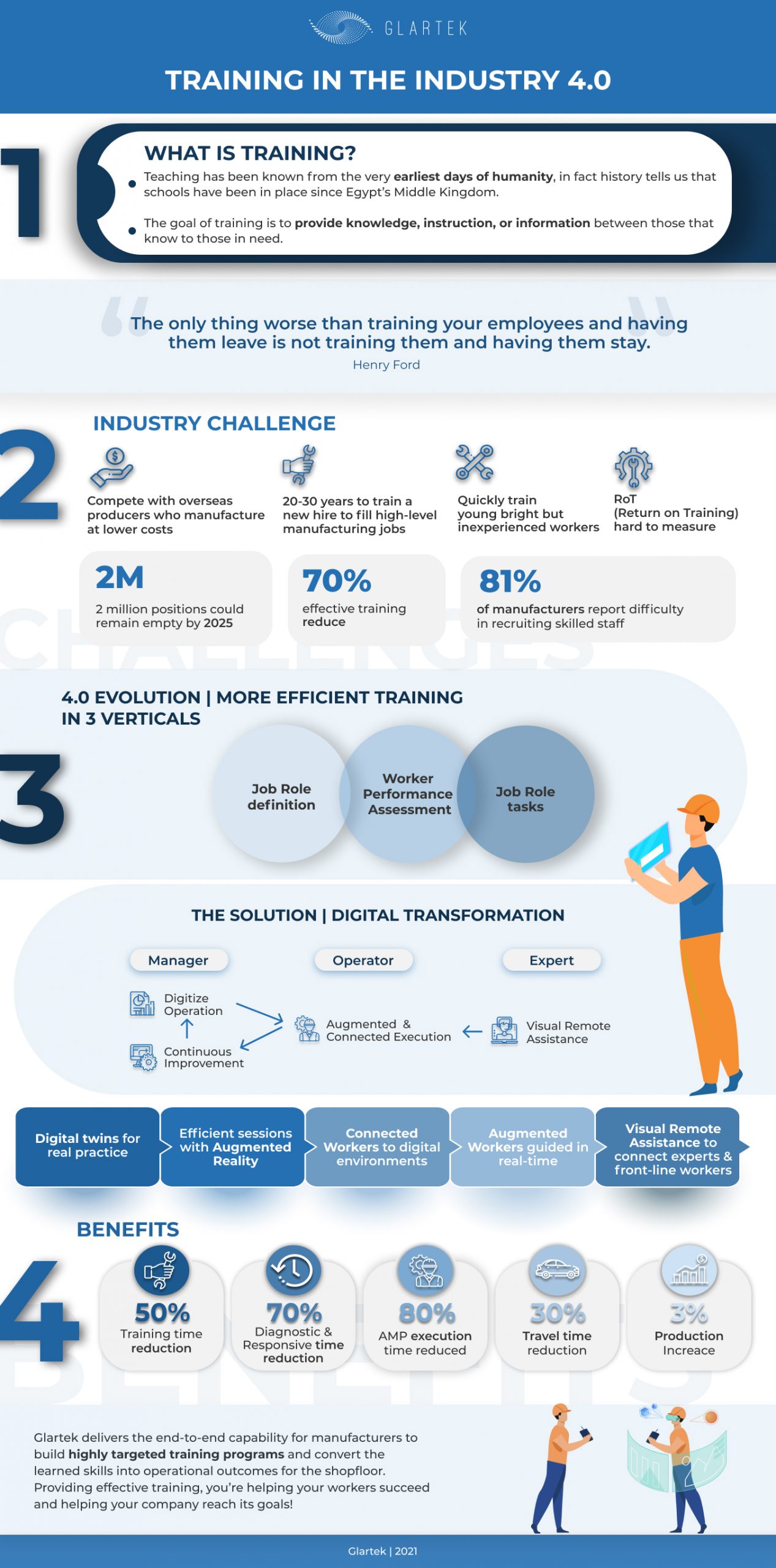
To ensure a successful outcome in the company’s investment in training, it is vital there is a seamless continuity between learning and practice. The Augmented & Connected Worker solution approaches this by ensuring that experts and trainers are always connected.
Whereas managers are approaching from an operational perspective by digitizing legacy paper or computer-aided Standard Operating Procedures used on the shop floors in conjunction with continuous improvement actions (like quality), the operator is able to simultaneously use his previous knowledge and seek guidance on demand thus ensuring continuous learning experience.