Quality Control
Maintenance, production, safety, quality, inspection, audits and much more procedures can be digitised with the new Augmented & Connected Worker solution.
What is a Quality Control?
A Shutdown & Turnaround process is a planning process in which an industrial facility goes through a scheduled shutdown in order to perform maintenance tasks that couldn’t be performed otherwise.
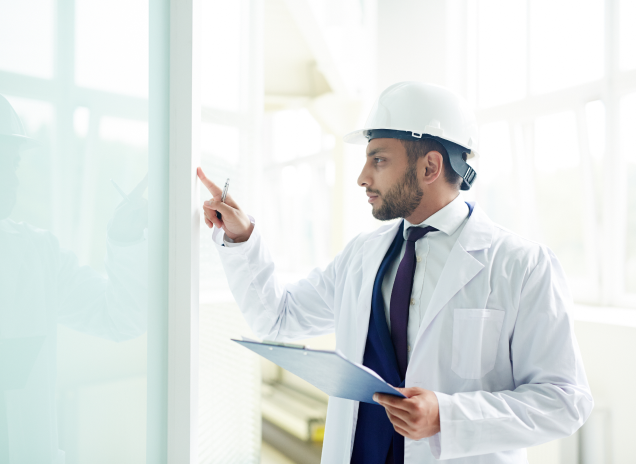
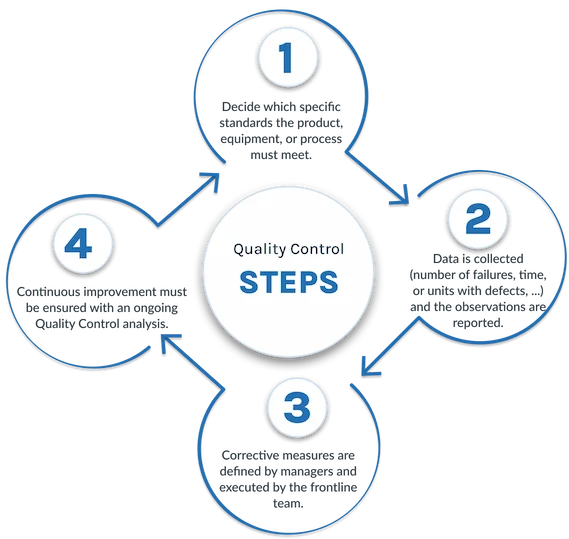
How is the Quality Control implemented?
Quality patterns are determined by the quality management team. These patterns are specified in processes and furthermore verified by field-workers accordingly. It can be implemented to verify the quality of products, equipment or even process supervision. Independently from the type of quality control executed, the process must follow 4 main steps, to ensure its efficiency.
How the Connected Worker platform can improve the procedure?
Augmented Reality (AR) Checklists
The platform helps with workflow organisation by enabling step-by-step augmented reality (AR) guides and real-time information to ensure the conformity of every operation.
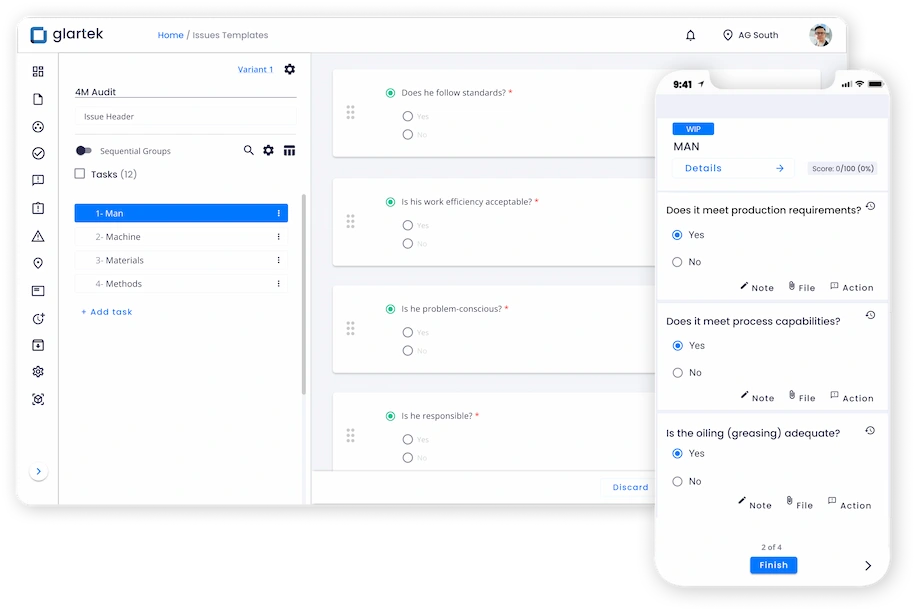
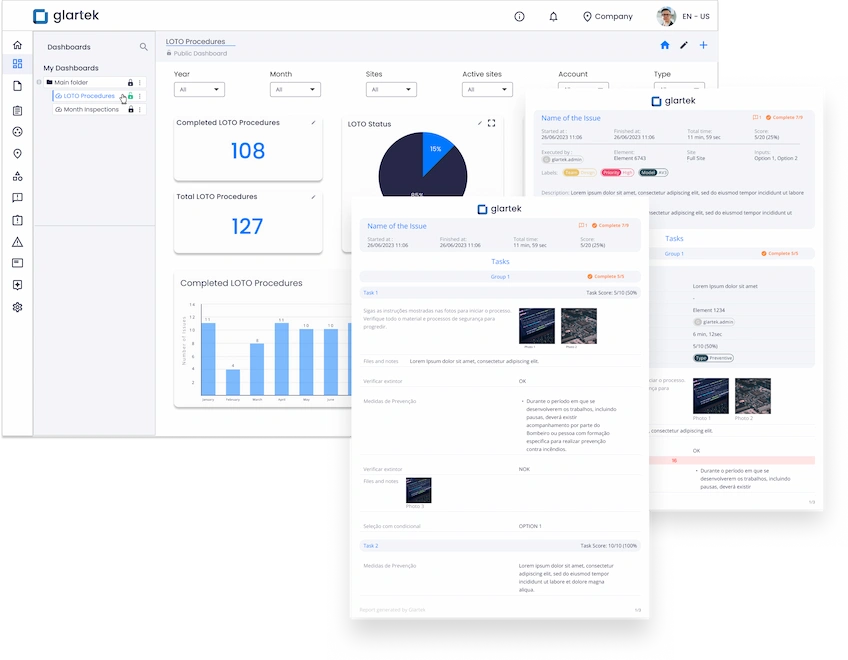
Analytics & Automated Reports
The process can be simplified with clearer instructions and easier access to workflow information. In addition, execution outputs are automatically recorded on digital platforms, which generate reports and dashboards of processes in real-time.
Benefits
Of going from Paper to Digital Procedures
By being provided with digital work instructions and AR Checklists, quality control execution is guaranteed. The quality control process can be executed by any worker with the correct information, which reduces workers’ needs. Additionally, continuous improvement will become a strategic pillar with regular analysis of the outputs extracted from quality control walks.
- REAL-TIME DATA
- UNIFORM EXECUTION
- CONTINUOUS IMPROVEMENT
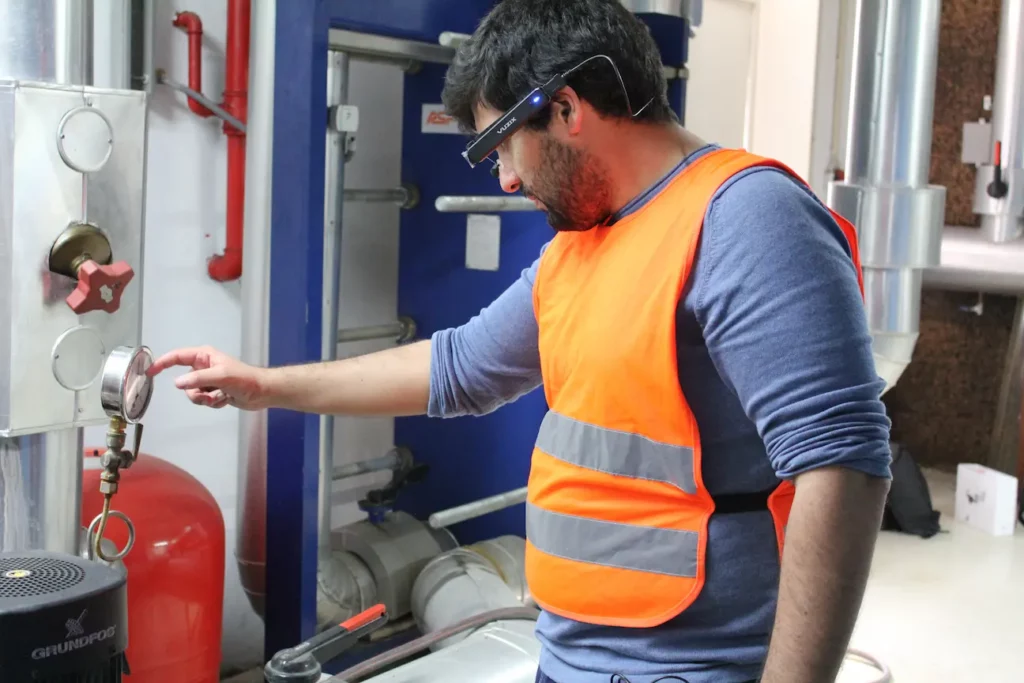