Training Procedure
Maintenance, production, safety, quality, inspection, audits and much more procedures can be digitised with the new Augmented & Connected Worker solution.
What is a Training?
Training is defined as the procedures in which people acquire new knowledge for a specific activity or goal. It includes both the person that is teaching, as well as the one learning.
The training goal is to increase knowledge, to enable workers to execute their tasks correctly, safely, and efficiently. Training is part of the daily life of any company, and has huge impact on results. Training sessions are usually executed when new workers arrive, on-the-job training and testing specific knowledge training.
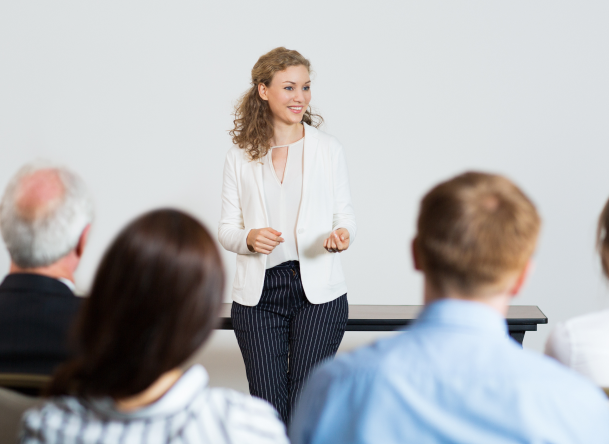
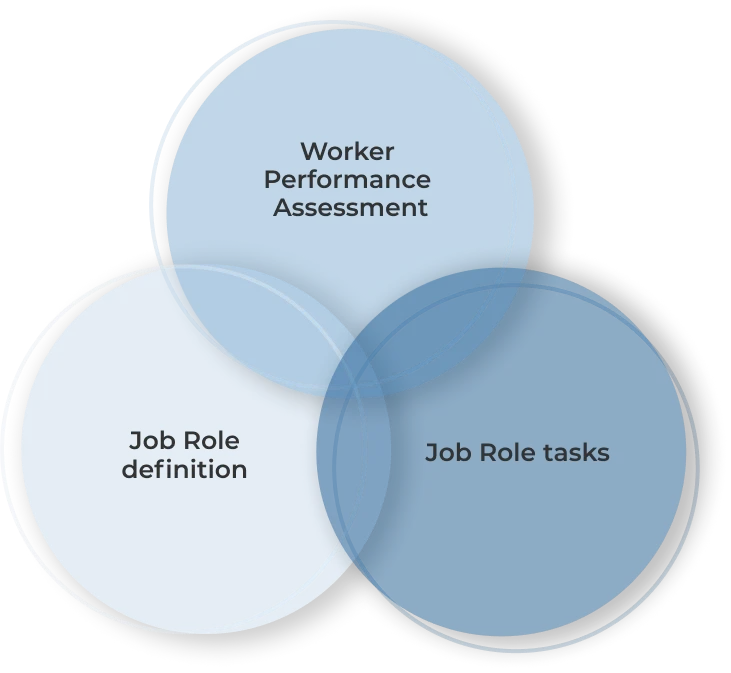
How is Training implemented?
All types of training include a passive and active learning methodology. In fact, it starts by acquiring more theoretical frameworks, and then applying them into a practical and realistic scenario to test the acquired knowledge. To achieve an efficient training session, 5 steps must be followed:
- Find and assess training needs.
- Set organizational objetives according to those needs.
- Create action plans with needed visuals, information, exercizes and others.
- Implement training.
- Evaluate and revise to verify the efficiency of the training.
How the Connected Worker platform can improve the procedure?
Digital Work Instructions
Training can be digitised in order to provide more mobility to the training session. Training that is supported by visual evidence, provided by the use of Augmented Reality (AR) helps to improve the learning curve.
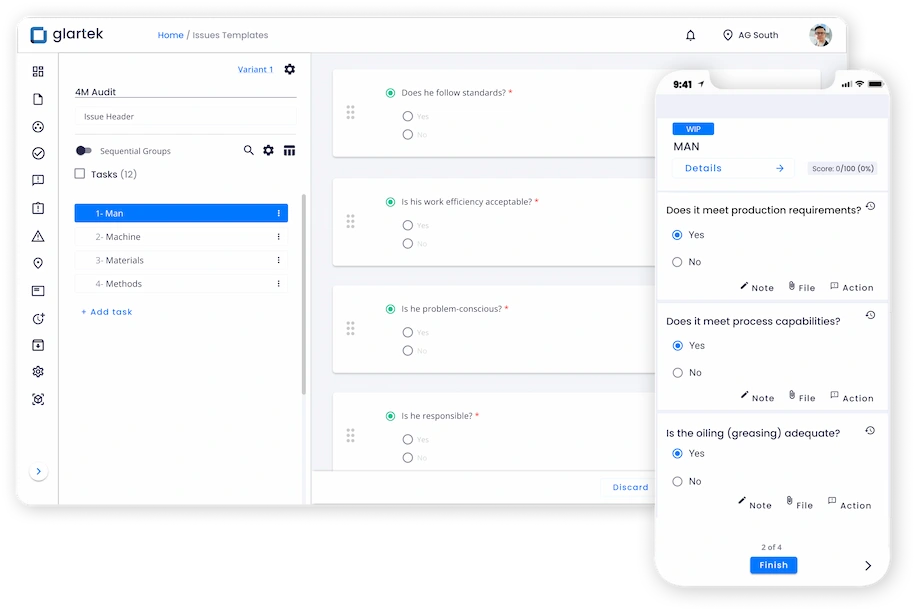
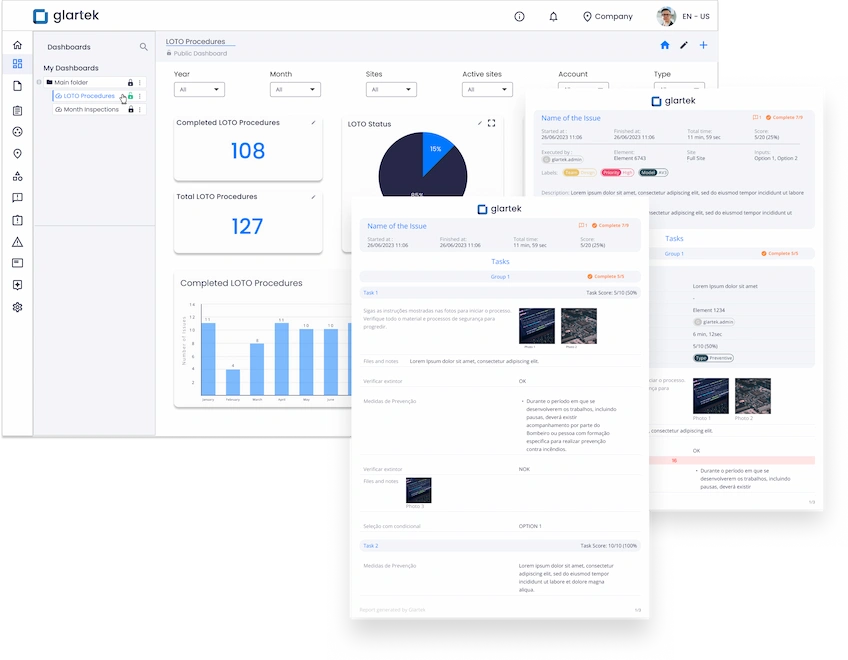
Automated Analytics & Reports
Automatic reports are generated so data is displayed in a visual way that facilitates both comprehension and analysis. It becomes easier to understand where and why problems happened and take corrective measures. These outputs extracted from digitalised training sessions improve decision-making by helping managers take faster decisions.
Benefits
Of going from Paper to Digital Procedures
With Industry 4.0 tools, knowledge retention is optimised and accelerated. Learning becomes more efficient and uniform, since training sessions are more practical, realistic and contextual. This reduces both error and the probability of putting workers or equipment in dangerous situations.
- KNOWLEDGE RETENTION
- UNIFORM EXECUTION
- FIRST TIME FIX-RATE
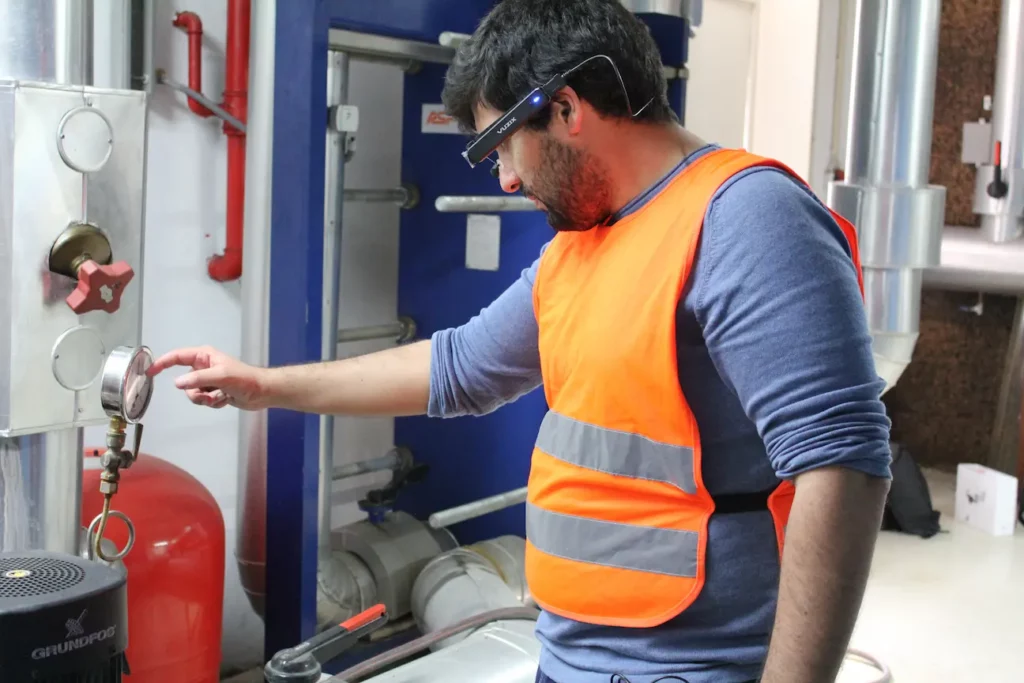
How can Glartek help?
Download our white paper to find everything about training in the Industry 4.0, and how Augmented Reality is helping with it.
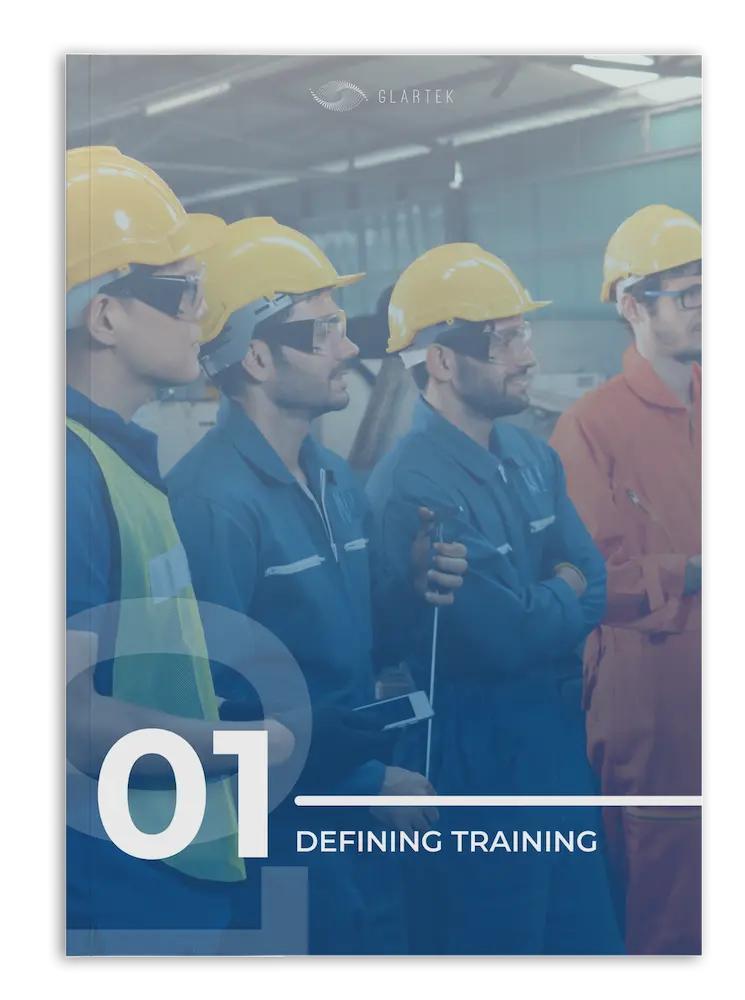