Production Startup Checklist
Maintenance, production, safety, quality, inspection, audits and much more procedures can be digitised with the new Augmented & Connected Worker solution.
What is a Production Startup Checklist?
The goal is to ensure that, while starting production, the workplace environment is clean, has everything that will be needed at the right place, and does not include any type of extra materials that may endanger production or workers. These safety measures must be executed by every operator before the production starts
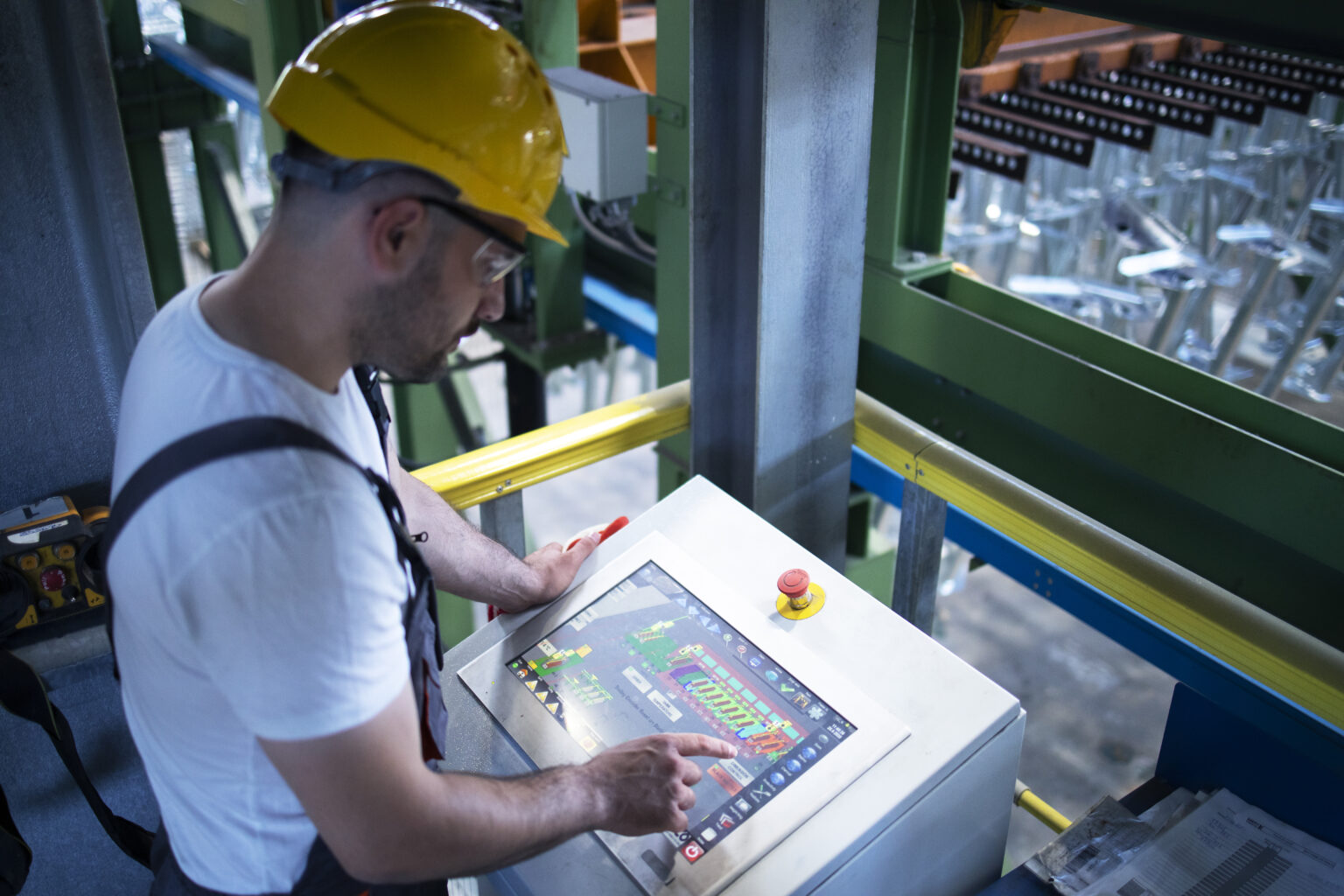
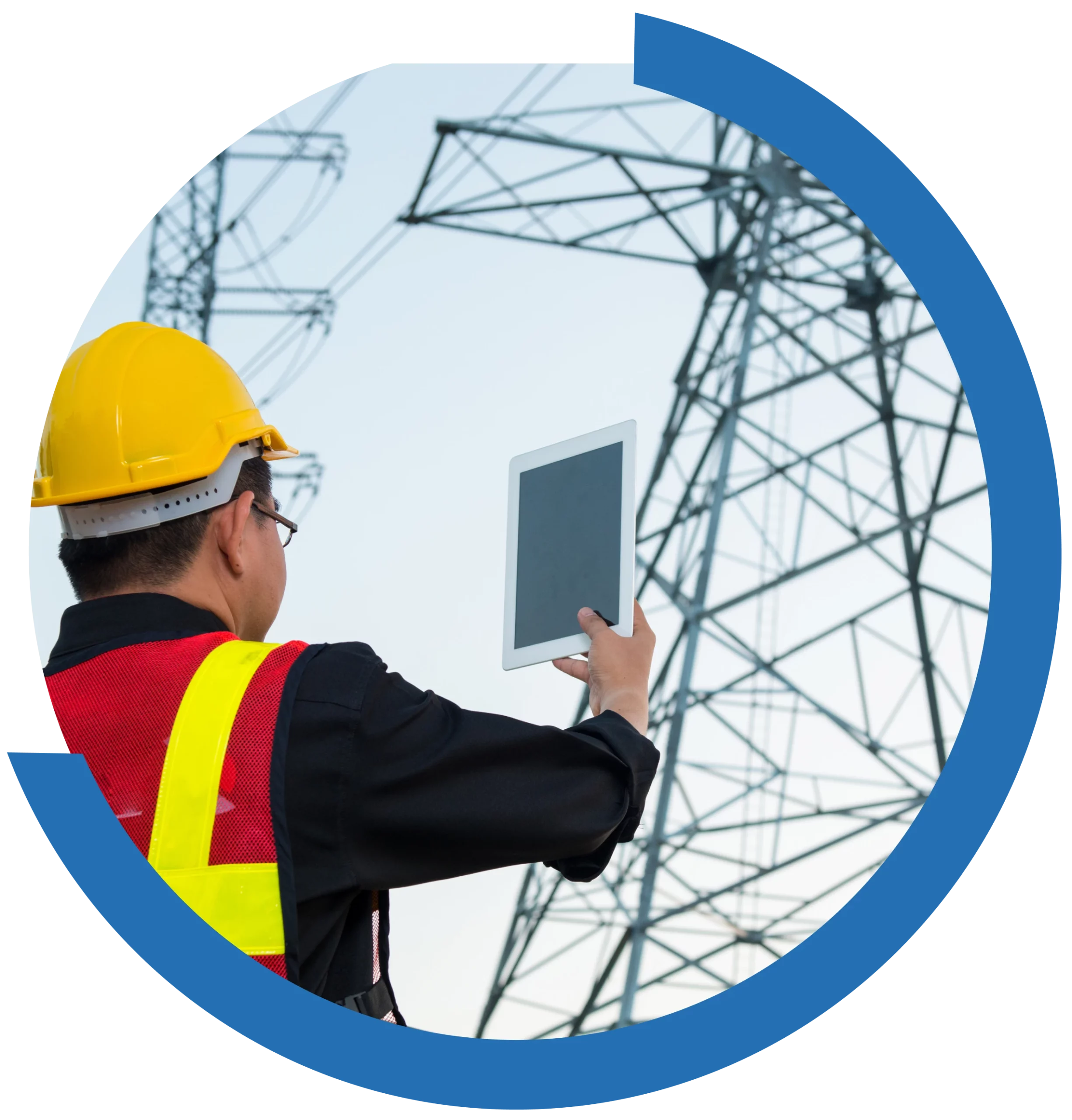
How is the Shutdown & Turnaround implemented?
The process usually includes a workflow to follow specific verifications across the workplace and equipment that must be verified by the worker before starting its work.Checklists are typically created in paper sheets. Workers register the execution of each task such as safety equipment verifications, if the right tools can be found near the workplace, or even if the previous worker has validated his tasks.
How the Connected Worker platform can improve the procedure?
Startup Permissions
A pre-initiation process can be created in the platform, under the form of a checklist. The workers will then be able to go through all the steps, accessing guides in real-time. This will guarantee that nothing is forgotten, and that time is not lost.
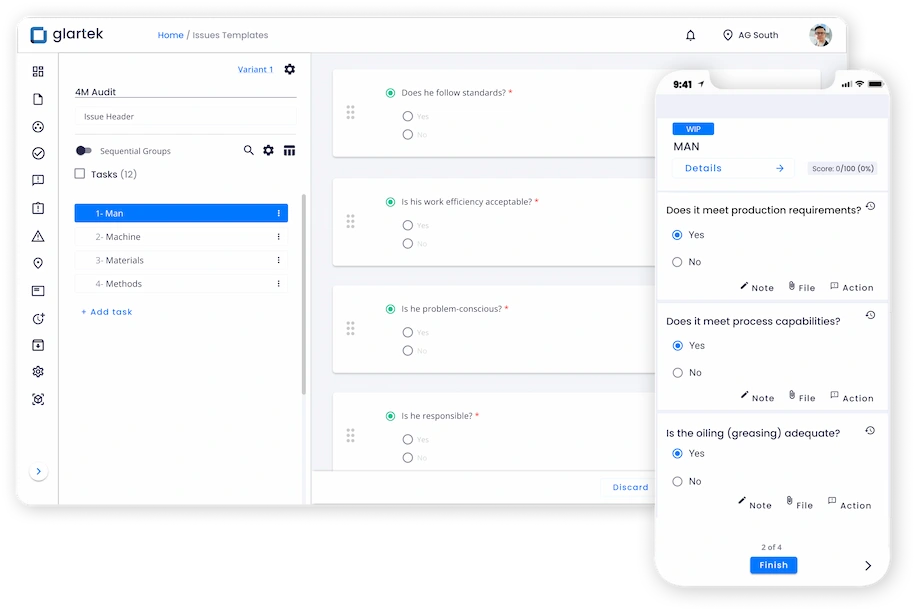
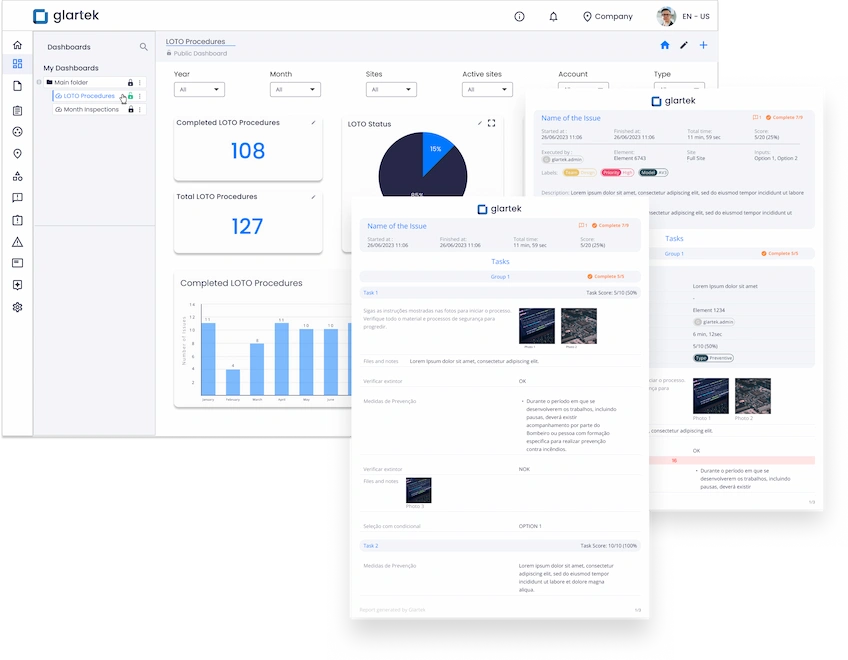
Automated tasks & reports
With digitised processes, it will be possible to analyse all the tasks that are required per process. It becomes much easier to automate actions that were once part of the process itself, such as some equipment or process verifications.
Benefits
Of going from Paper to Digital Procedures
Besides improving and facilitating execution safety and quality, process digitalisation concedes managers with more visibility and control over processes. Not only, the overall execution is more efficient, due to a valuable support tool conceded to field workers. Additionally, decision-makers can reduce and automate verification tasks that do not always require human effort to be executed.
- MORE EFFICIENCY
- MORE CONTROL
- IMPROVED SECURITY
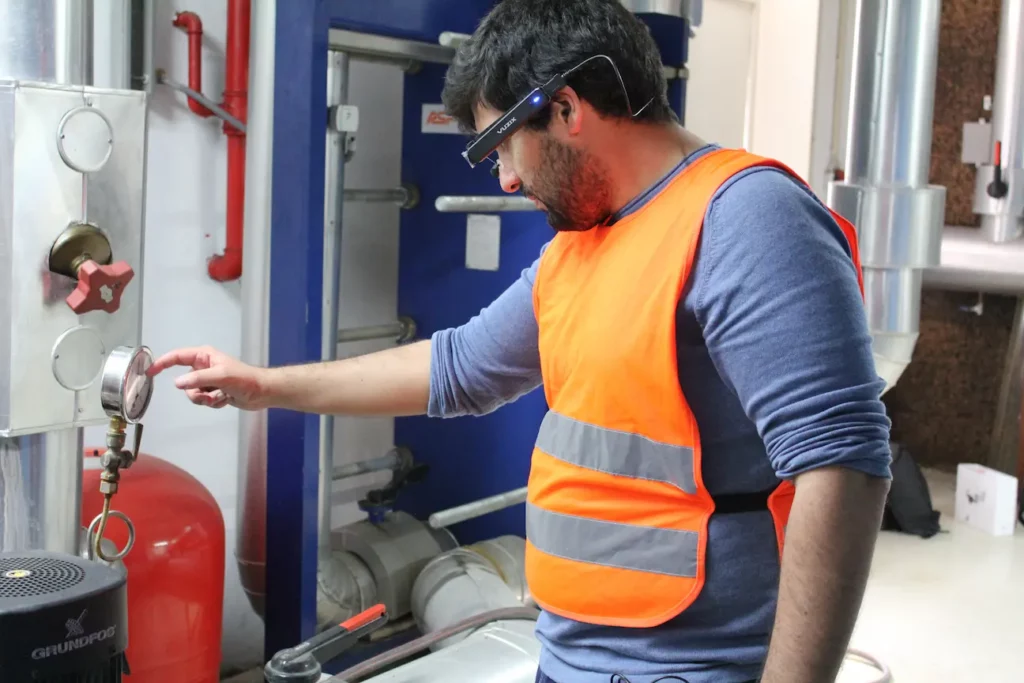