Layered Process Auditing (LPA)
Maintenance, production, safety, quality, inspection, audits and much more procedures can be digitised with the new Augmented & Connected Worker solution.
What is a LPA Procedure?
LPA (Layered process audit) are processes that aim to increase the quality of finished products, by auditing the production process and inspecting how products are made, instead of just observing the finished version. This process aims at conducting regular internal audits, at every hierarchical level. The in-depth analysis is part of a Quality Management System that helps organizations detect gaps and areas of improvement in the company.
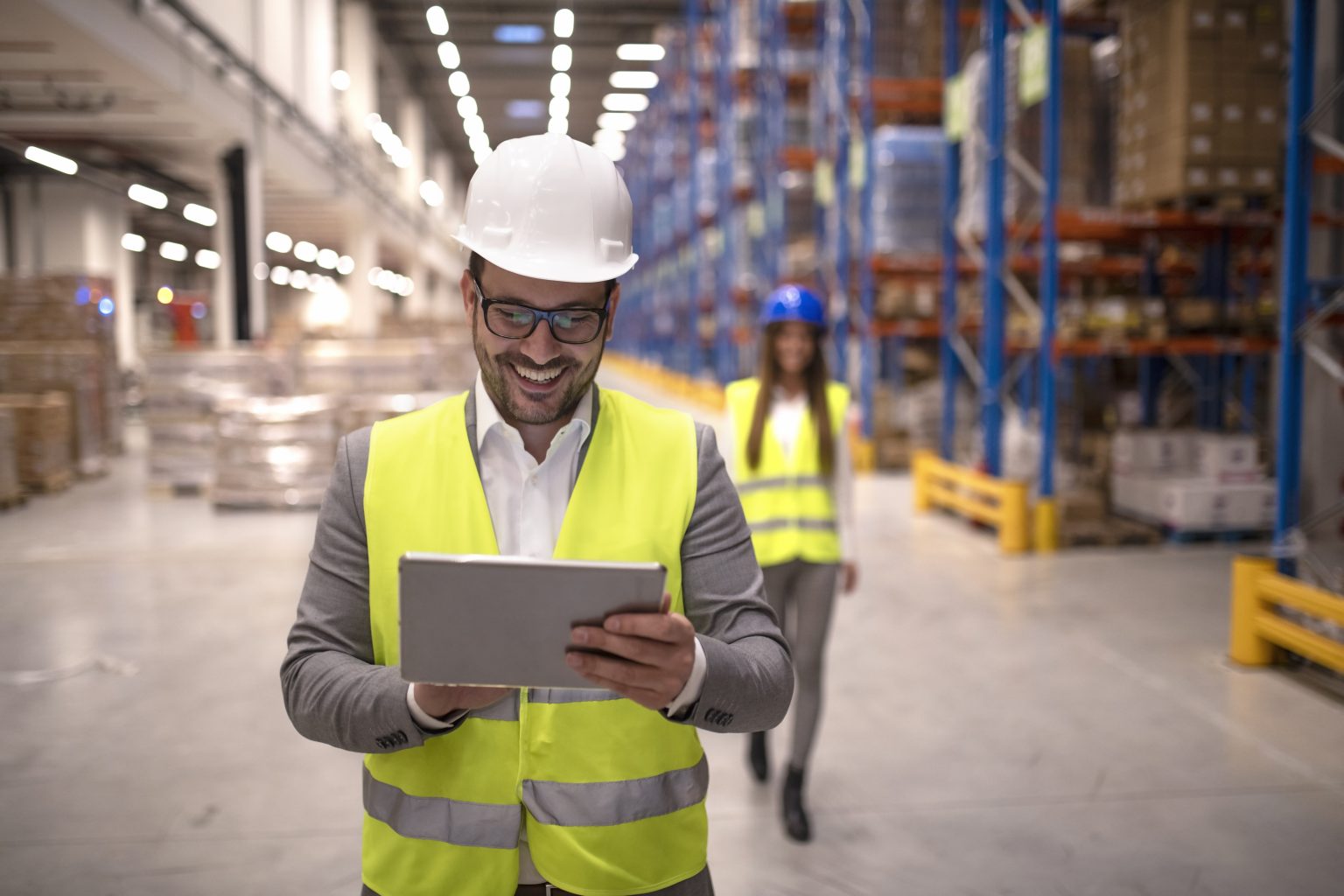
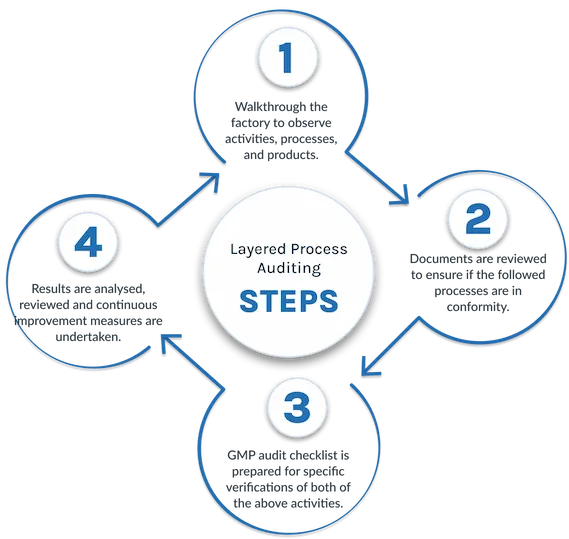
How is the Shutdown & Turnaround implemented?
How the Connected Worker platform can improve the procedure?
Digital Work Instructions
Digital platforms allow businesses to centralize data and create digital checklists to support the process. These solutions are available for different management layers, providing field workers with information to execute processes and provide feedback. Simultaneously, it allows management teams to have more control over everything that is occurring on the shop floor.
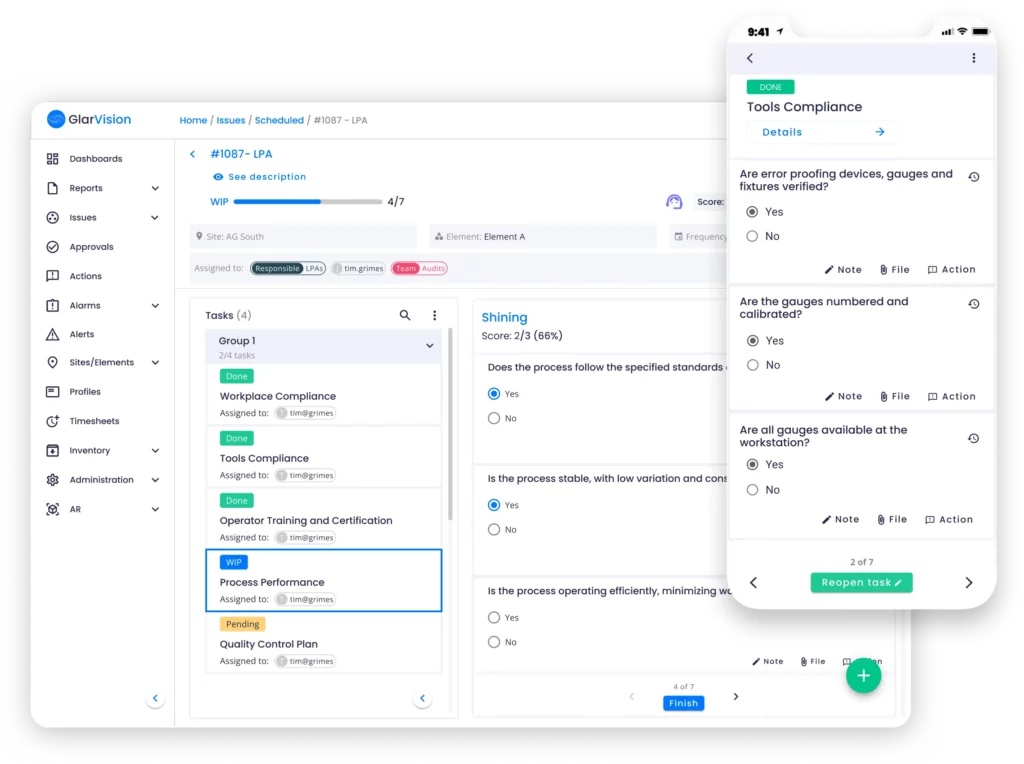
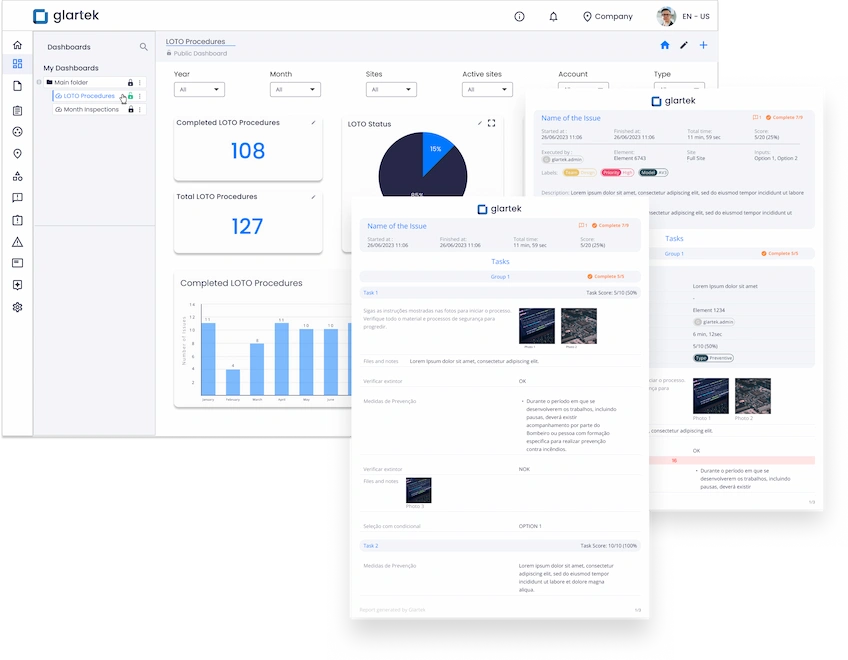
Output data & Analysis
Automatic reports and dashboards are generated according to execution. Data is displayed in a visual format that facilitates both comprehension and analysis. As a result, it becomes easier to understand where and why problems have taken place and to take corrective measures.
Benefits
Of going from Paper to Digital Procedures
Process digitalization efficiently combined with IoT increases visibility and control over any process. The solution allows workers to easily access information and guides about the process, and, data from equipment behavior using a see-through screen that superimposes digital elements and the real industrial environment. Additionally, by collecting visual evidence during task execution, it is possible to confirm the correct execution and reduce the possibility of unexpected errors.
- INCREASED VISIBILITY
- UNIFORM EXECUTION
- MORE CONTROL
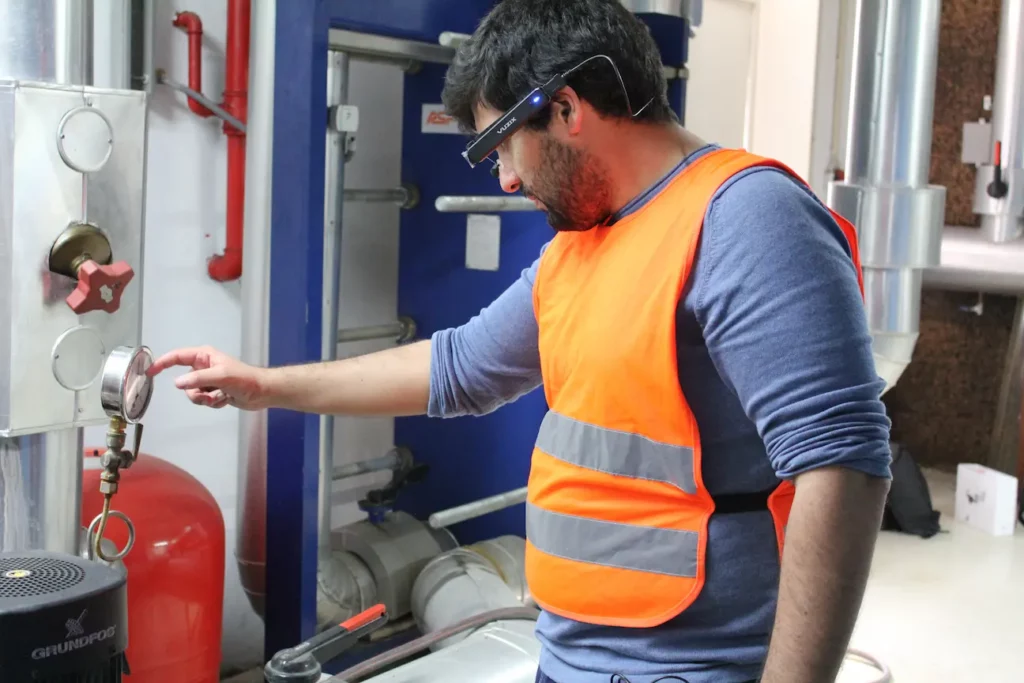
How can Glartek help?
The Augmented & Connected Worker is an unique platform that combines process digitalization with IoT data extracted from the factory floor. The platform organizes workflows according to different needs and users. Not only does the platform deploy valuable inputs but also generates automatic reports that gather different observations and notes to inform the decisions of different hierarchical levels. This facilitates decision-making but also allows it to be more concise.
REQUEST YOUR LPA PROCEDURE TEMPLATE!
Download your detailed LPA procedure template and import it into the Augmented & Connected Worker platform. You can also read our blogpost and learn more about how to migrate LPA Audits from paper to digital.
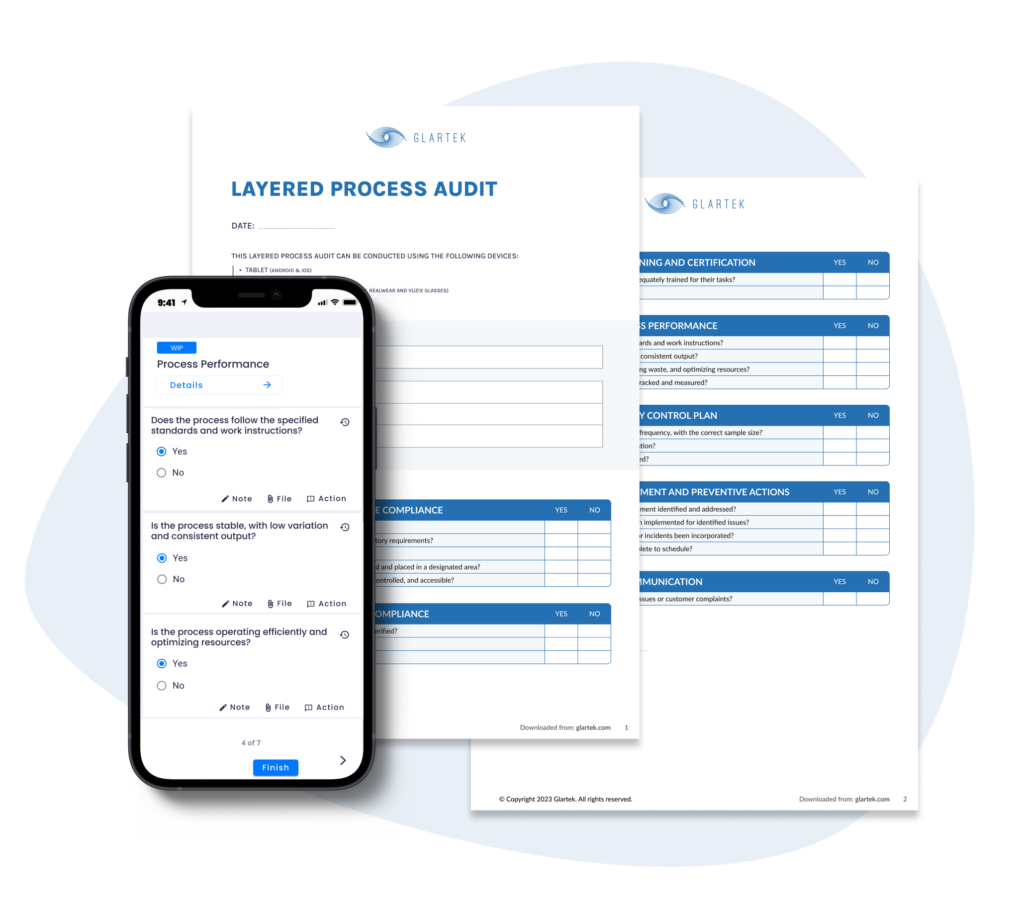