Preventive Maintenance
Maintenance, production, safety, quality, inspection, audits and much more procedures can be digitised with the new Augmented & Connected Worker solution.
What is a Preventive Maintenance?
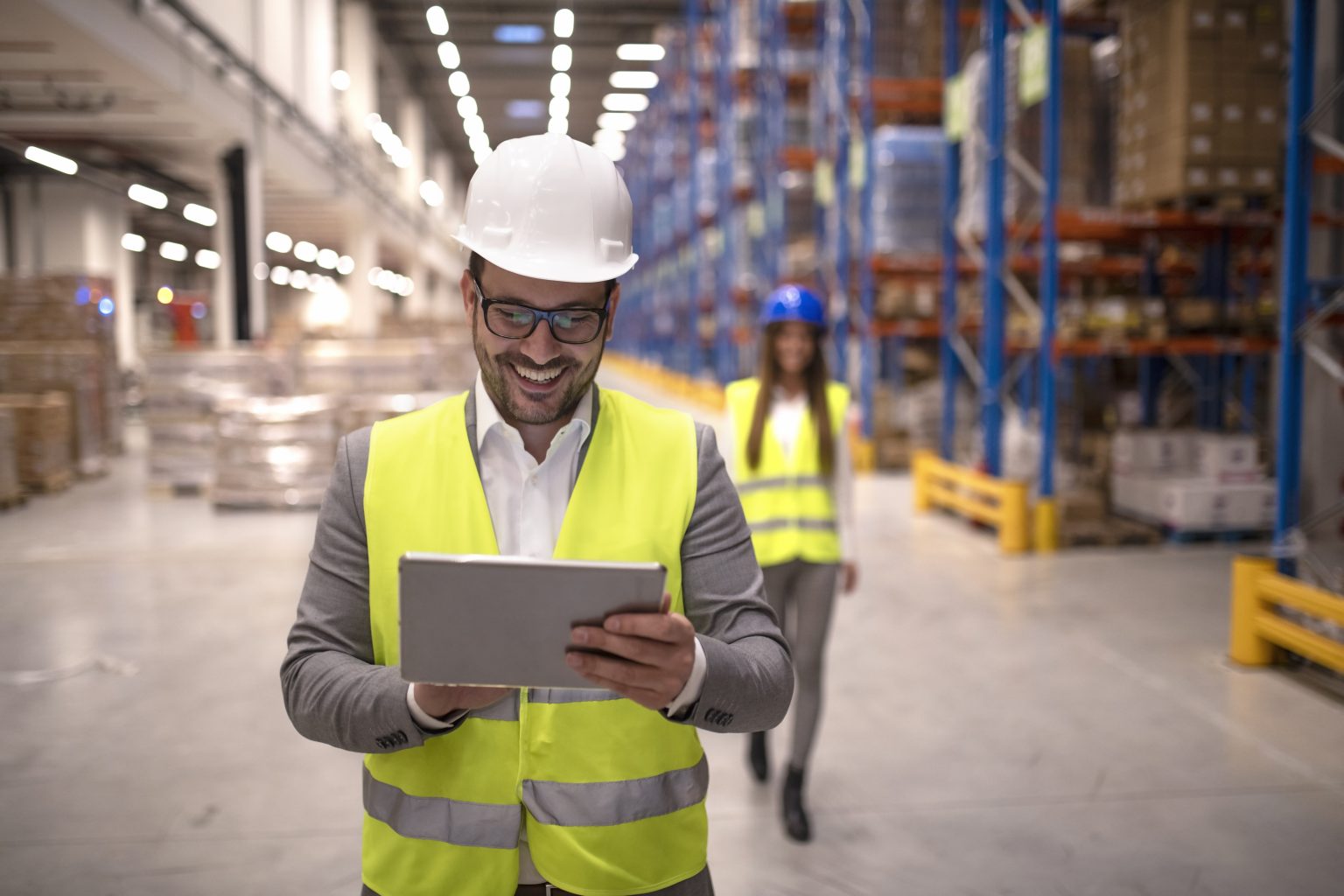
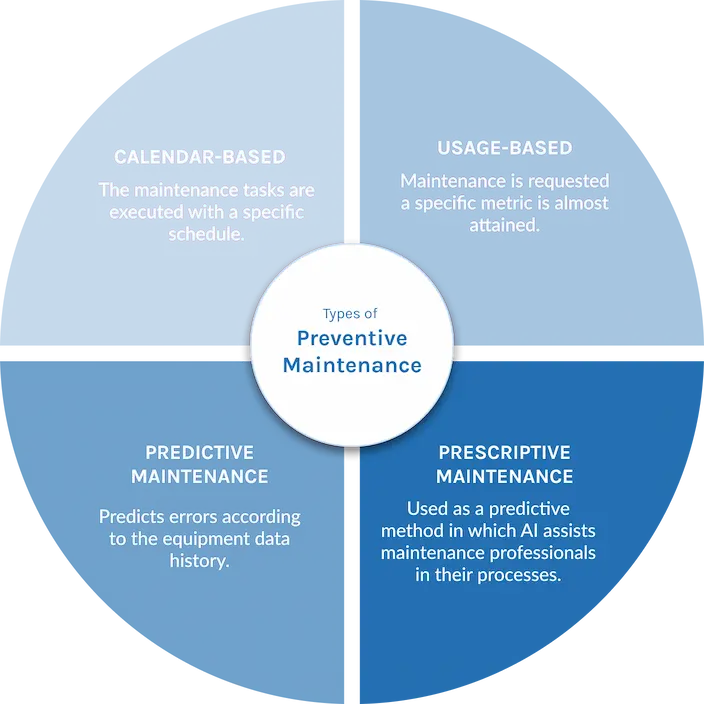
How is the Preventive Maintenance implemented?
This type of maintenance is a regular process that is scheduled according to equipment working hours or lifetime. Workers engage in regular processes to avoid breakdowns before they happen. These tasks can include replacing parts, verifications, and others, even if not needed.
There are four different types of preventive maintenance that require specific types of know-how, each one based on different indicators that trigger the alert to conduct preventive maintenance.
- Calendar Based Maintenance
- Usage Based Maintenance
- Prescriptive Maintenance
- Predictive Maintenance
How the Connected Worker platform can improve the procedure?
Digital Work Instructions
Processes can be digitized in platforms that organize the process, deploying a calendar with daily and future tasks for each worker to execute. It will allow not only to allocate tasks according to specific profiles, as well as track results, and control executions in real-time.
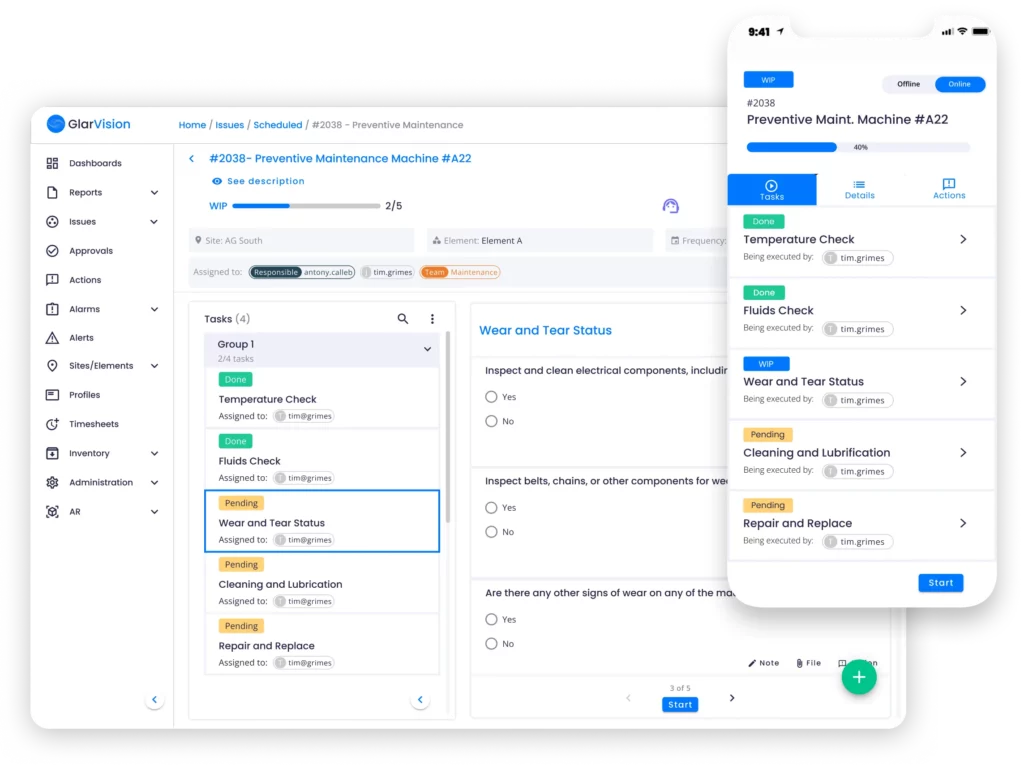
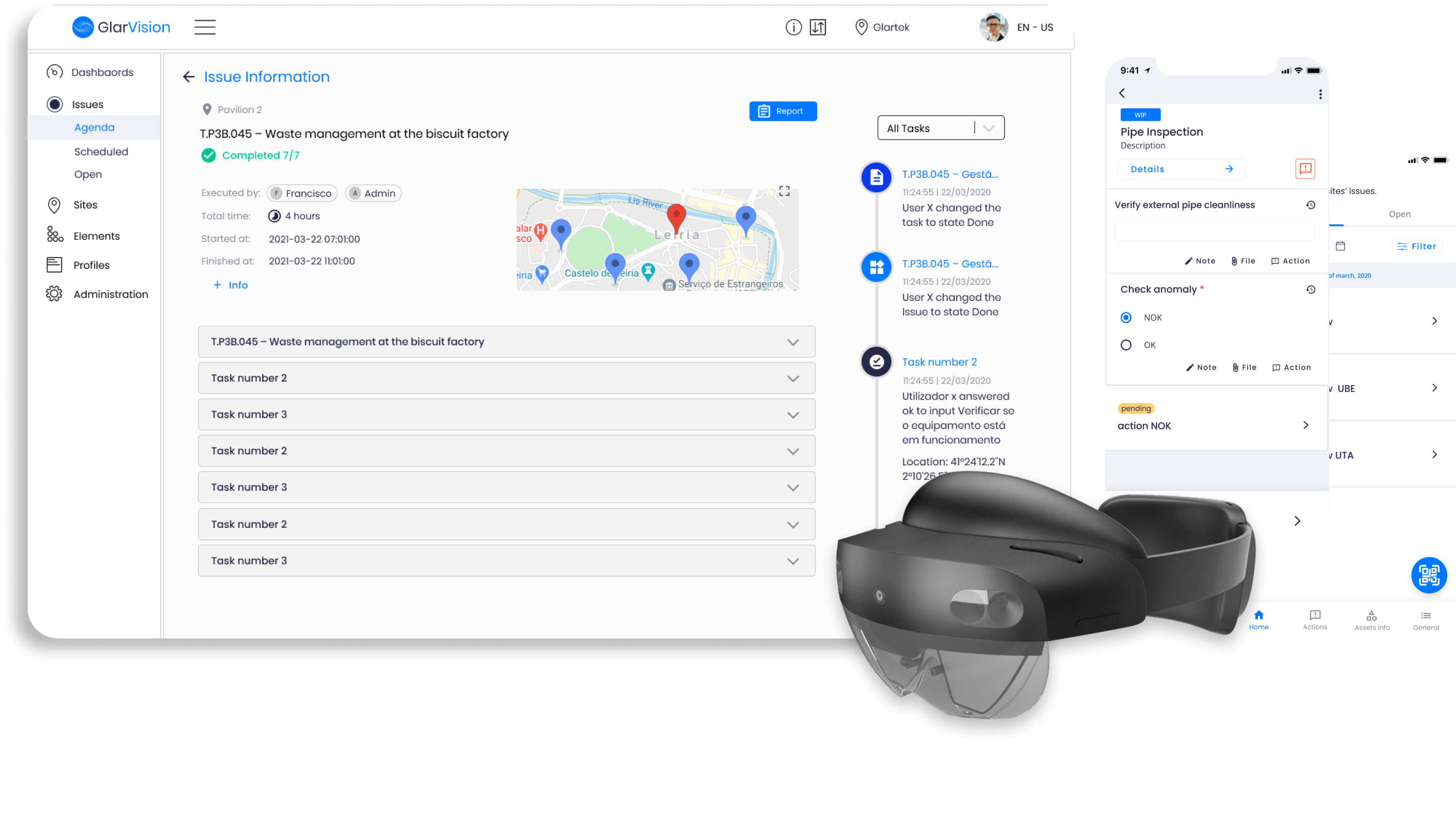
IoT Data
In addition, IoT information can be extracted from the equipment. Connections can be created and data becomes visible. For example, about the equipment behavior regarding temperatures, humidity and others. This places companies one step further to predictive maintenance.
Benefits
Of going from Paper to Digital Procedures
Processes will be executed in less time and will demand less costs, hence tools are provided to guide workers through maintenance tasks. By starting to engage in predictive maintenance processes, costs are highly reduced. Additionally, by engaging in predictive maintenance, there is less time wasted with unnecessary maintenance, when equipment is still in a good state, or less time with downtime for maintenance tasks to be applied.
- COST REDUTION
- ERROR REDUTION
- EFFICIENCY INCREASE
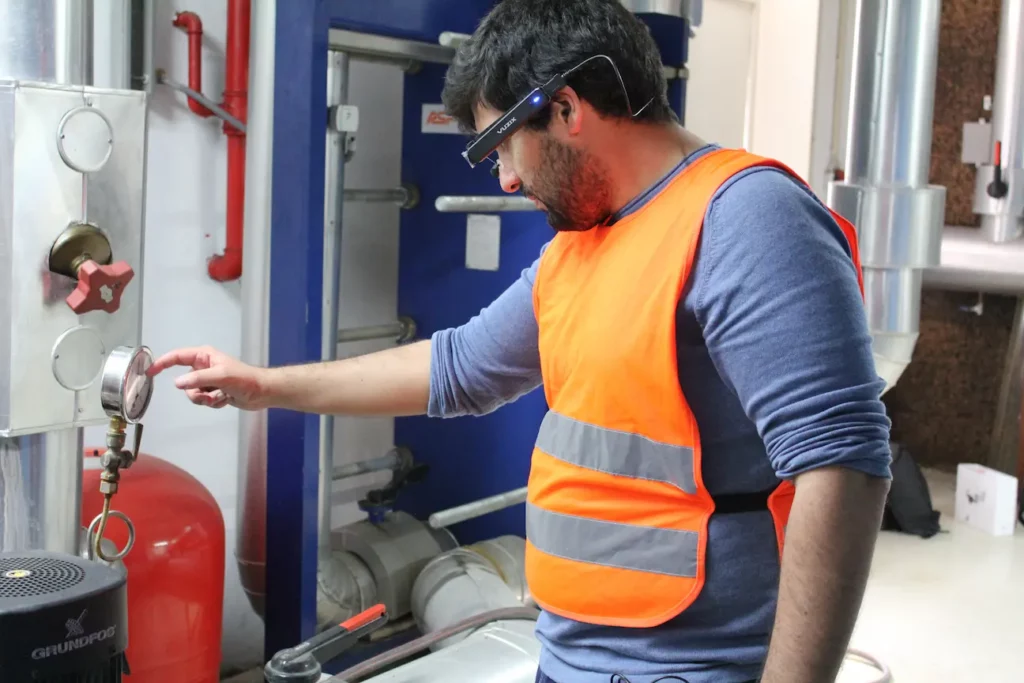
How can Glartek help?
The Augmented & Connected Worker platform allows digitizing processes. Altogether, this facilitates maintenance tasks hence it provides any worker with tools, both guides, and remote assistance, to execute any task. This reduces the need to have highly experienced specialists to execute maintenance. Additionally, with our solution, your company can take the next step into the maintenance quality, engaging in a predictive maintenance method supported by IoT data extracted with our product to an IoT platform.
REQUEST YOUR PREVENTIVE MAINTENANCE TEMPLATE!
Download your detailed procedure template and import it into the Augmented & Connected Worker platform. You can also read our blogpost and learn more about how to migrate Preventive Maintenance procedures from paper to digital.
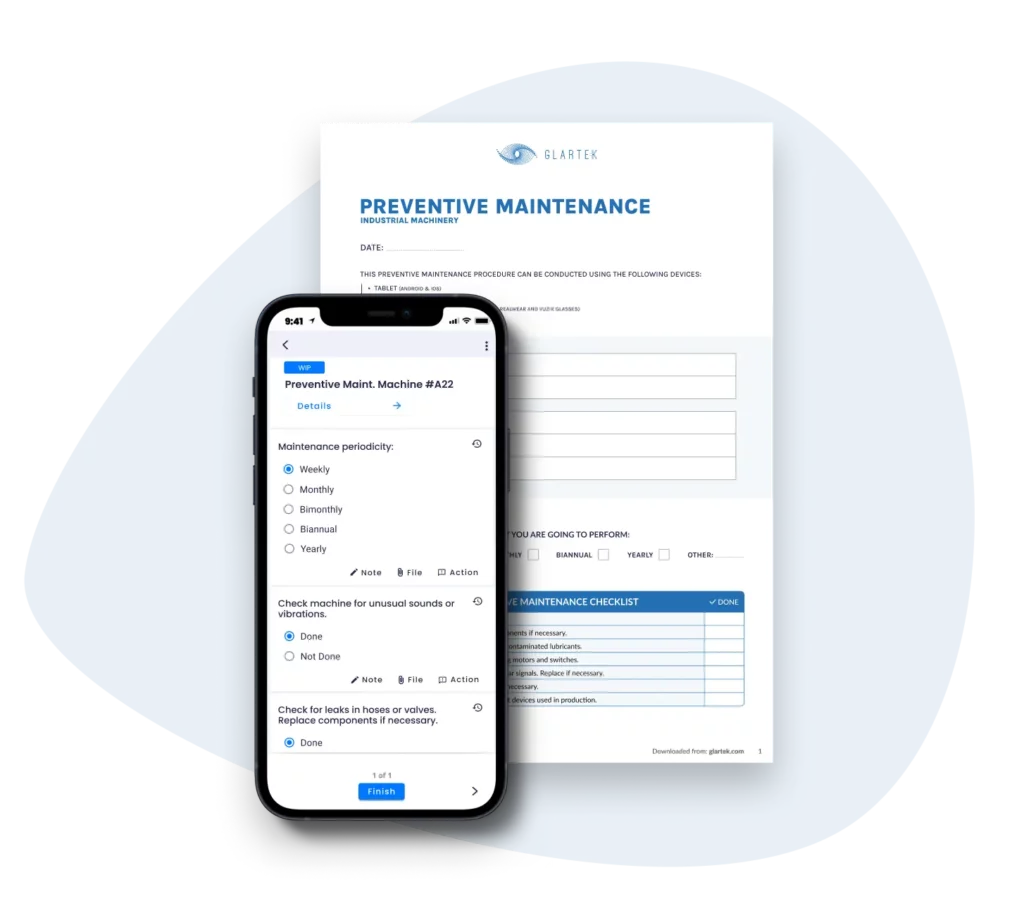