Root Cause Analysis
Maintenance, production, safety, quality, inspection, audits and much more procedures can be digitised with the new Augmented & Connected Worker solution.
What is a Root Cause analysis?
A Shutdown & Turnaround process is a planning process in which an industrial facility goes through a scheduled shutdown in order to perform maintenance tasks that couldn’t be performed otherwise.
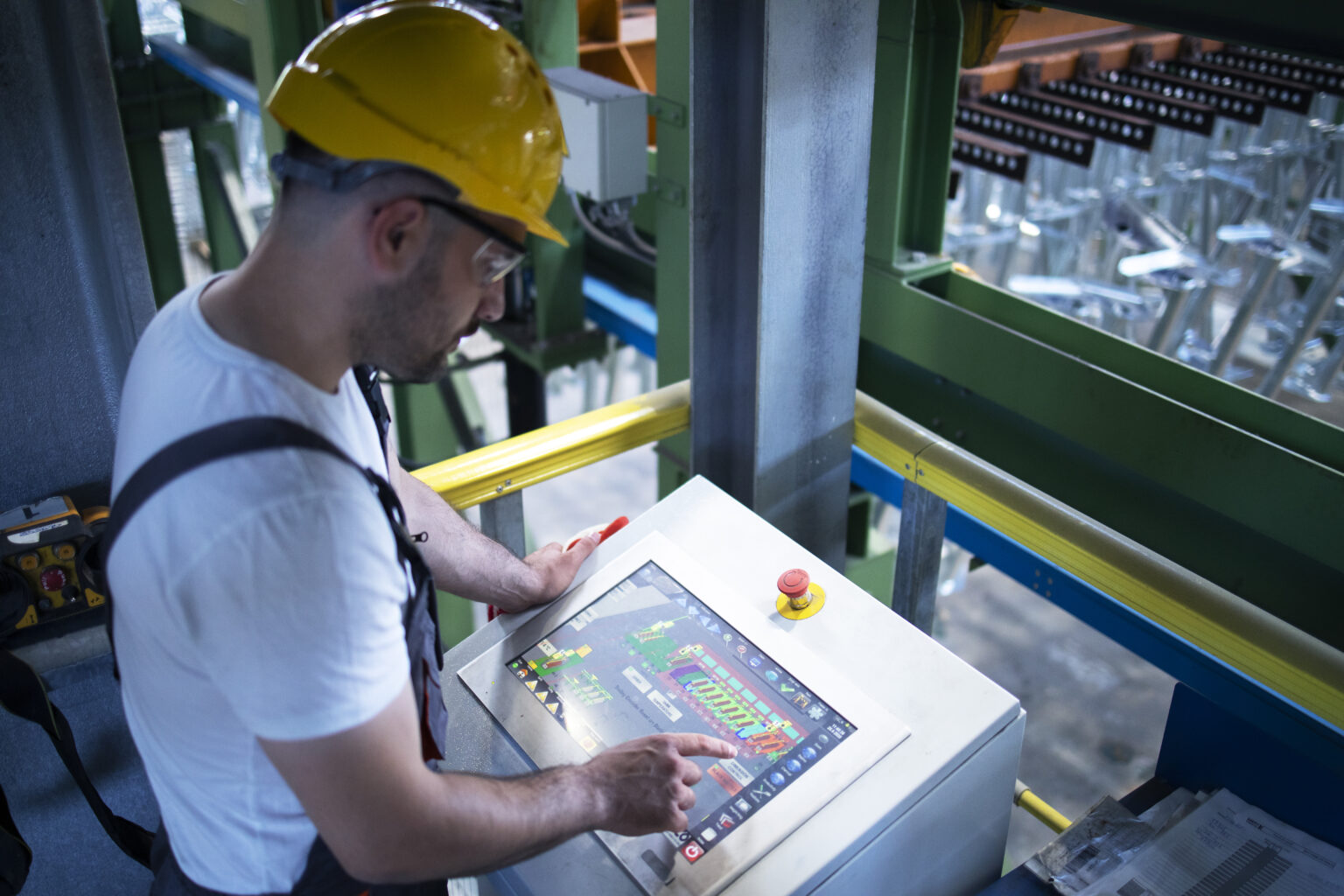
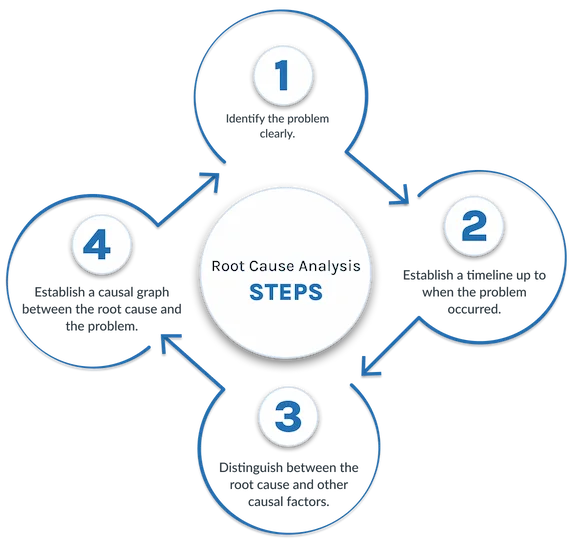
How is the Root Cause Analysis implemented?
Root Cause Analysis (RCA) helps workers finding the cause of a problem, looking for its origin, and ensure it is not repeated.
Each one of the 4 steps demands a specific inside procedure. Root Causes for a specific event are not always easy to find. Therefore, ensuring good tools to support workers on these operations is key to success.
How the Connected Worker platform can improve the procedure?
Digital Work Instructions
Root Cause Analysis can be digitised and track the progress of the process. Thus, the first step is to digitise all the processes necessary for the procedure.
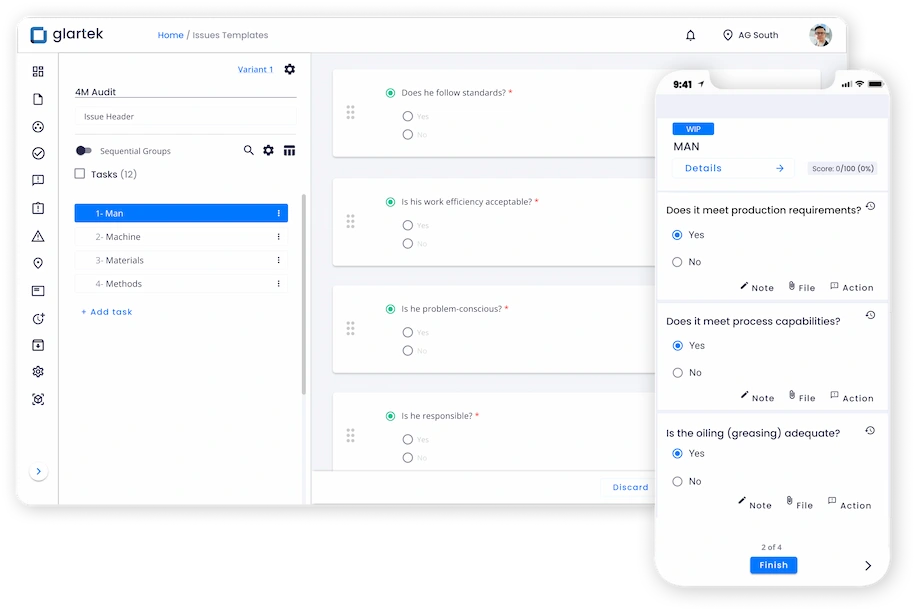
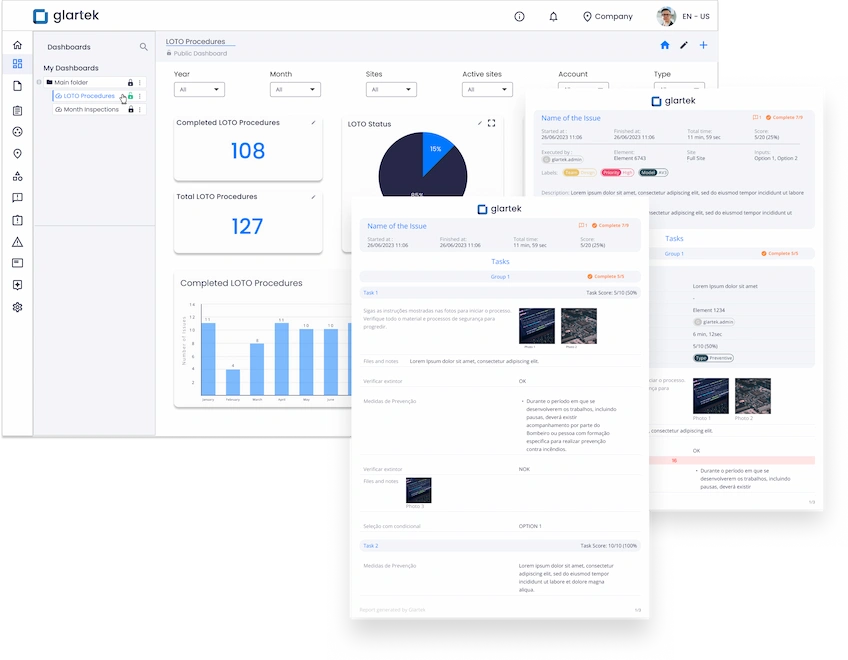
Advanced Reports & analytics
Once the processes are completed and documented, the platform provides advanced reports and metrics to facilitate business critical decision making.
Benefits
Of going from Paper to Digital Procedures
RCA processes identify issues that decrease efficiency and wasted raw material, human resources and financial resources. Having the correct RCA strategy leads to increased productivity and costs savings.
- KNOWLEDGE RETENTION
- UNIFORM EXECUTION
- TIMELINE ESTABLISHED
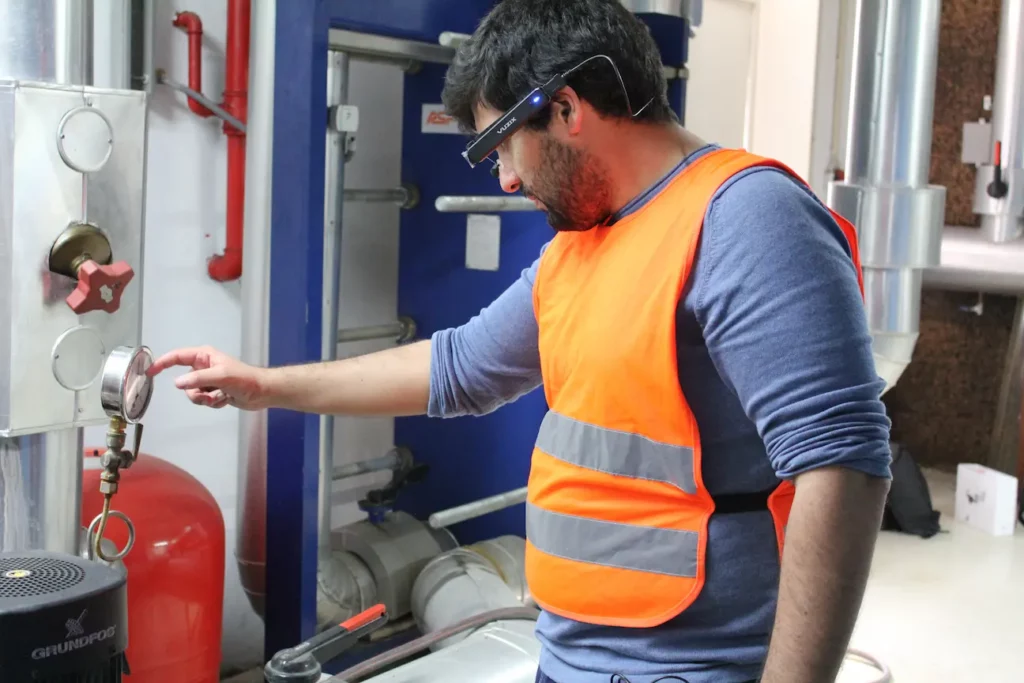